The advantage of adding a variable frequency drive is that changes in the load have no effect on motor efficiency. We use the motor nameplate efficiency value when calculating energy use at any load.
We use the same formulas to compute energy use. The total energy use is 253,635 kWh, compared to 321,339 before.
The annual cost after adding the variable frequency drive is calculated by adding the demand charges and the standard energy charges. Demand charges are $2,430 and standard energy charges are $10,145 for an annual total of $12,575.
The annual energy costs without the variable frequency drive was $15,338. The addition of an variable frequency drive yields an Annual Cost Savings of $2,763.
It is now possible to compute simple payback and look at the lifetime costs.
We use the same formulas to compute energy use. The total energy use is 253,635 kWh, compared to 321,339 before.

The annual cost after adding the variable frequency drive is calculated by adding the demand charges and the standard energy charges. Demand charges are $2,430 and standard energy charges are $10,145 for an annual total of $12,575.
The annual energy costs without the variable frequency drive was $15,338. The addition of an variable frequency drive yields an Annual Cost Savings of $2,763.
It is now possible to compute simple payback and look at the lifetime costs.
Manufacturers of medium and large VFDs typically provide information on the requirements for power cables connecting the inverter to the AC motor and from the VFD isolation transformer to the converter. Cable and panel grounding recommendations are also included. Cable supplier catalogs and Web sites provide detailed information, but not necessarily everything needed to determine if the VFD manufacturer's recommendations are being met. This paper provides typical requirements, reasons for those requirements, and some useful insights to help the reader bridge the gap between VFD supplier requirements and cable supplier published data.
Despite the fact that variable frequency drives generate a large amount of harmonics and heat, they would not be as widely used and popular as they are today if they did not have significant economic benefits.
Electrically, variable frequency drives run at a high power factor. Any class of induction motors usually has a low power factor at half and three-quarters load (0.75 to 0.85). This actually decreases the life of the motor, because the unnecessary increase in current overheating the winding insulation. Variable frequency drives bypass this problem by running the load at a frequency below the fundamental.
The most obvious reason to procure a variable frequency drive is speed control. This is usually done for process, operation, and economic benefits. One economic benefit comes from the reduction of maintenance when using a variable frequency drive, especially not having to deal with the DC motor carbon brushes or mechanical speed-control gearboxes (transmissions). The most obvious economic benefits of variable frequency drives occur with pumps and fans. The power that a pump or fan consumes is directly proportional to the cube of the velocity. This means if an operator can run a fan at 80% of full speed, it theoretically uses 51% of full load power.
Electrically, variable frequency drives run at a high power factor. Any class of induction motors usually has a low power factor at half and three-quarters load (0.75 to 0.85). This actually decreases the life of the motor, because the unnecessary increase in current overheating the winding insulation. Variable frequency drives bypass this problem by running the load at a frequency below the fundamental.
The most obvious reason to procure a variable frequency drive is speed control. This is usually done for process, operation, and economic benefits. One economic benefit comes from the reduction of maintenance when using a variable frequency drive, especially not having to deal with the DC motor carbon brushes or mechanical speed-control gearboxes (transmissions). The most obvious economic benefits of variable frequency drives occur with pumps and fans. The power that a pump or fan consumes is directly proportional to the cube of the velocity. This means if an operator can run a fan at 80% of full speed, it theoretically uses 51% of full load power.
There are many important considerations for all industrial electronic equipment; however, the two most important are cooling and line power quality.
1) Cooling: variable frequency drive control units should be installed in locations where the maximum ambient temperature does not exceed 40 [degrees] C (104 [degrees] F). This is a common temperature rating for most units. If higher ambients are expected, derating of the variable frequency drive may be required.
You should avoid installing units in mezzanines, direct sunlight, or near external heat sources because these locations usually have unpredictable temperature rises. If you must install variable frequency drives in such areas, take steps to provide necessary cooling.
Proper cooling of the variable frequency drive's heat sink is essential for successful operation. Wall-mounted units employ a "chimney effect" for cooling of the heat sink and must be mounted against a smooth, flat, vertical surface. If a wall-mounted unit is to be installed in a free-standing position, then plywood or a sheet of metal should be fastened to the back of the unit to ensure that chimney-effect cooling will be achieved. Larger free-standing variable frequency drives require minimum clearances around them for sufficient air flow to circulate through them, assuring adequate cooling.
Altitude affects the heat dissipation capability of the heat sink and units in locations at 3300 ft (1000 m) above sea level must be derated. A common rule of thumb is a 2% derating for every 1000 ft above the 3300 ft altitude level.
2) Supply line power quality: The line voltage (supply) to the VFD input should not vary plus or minus 10% because most VFDs will trip via a protective fault. This voltage stability should be considered when running conductors to the VFD and voltage drops should be calculated for long runs.
Very often external control signals are used to start/stop and control the speed of a variable frequency drive. Control signal types can vary depending on the application. It's not unusual to have a 115V or 24V control circuit for start commands and a 4-20mA or 0-5VDC signal for speed control. These control signals must be run independently of each other as well as separate from any power wiring. Induced noises can produce erratic VFD behavior that is very difficult to troubleshoot.
1) Cooling: variable frequency drive control units should be installed in locations where the maximum ambient temperature does not exceed 40 [degrees] C (104 [degrees] F). This is a common temperature rating for most units. If higher ambients are expected, derating of the variable frequency drive may be required.
You should avoid installing units in mezzanines, direct sunlight, or near external heat sources because these locations usually have unpredictable temperature rises. If you must install variable frequency drives in such areas, take steps to provide necessary cooling.
Proper cooling of the variable frequency drive's heat sink is essential for successful operation. Wall-mounted units employ a "chimney effect" for cooling of the heat sink and must be mounted against a smooth, flat, vertical surface. If a wall-mounted unit is to be installed in a free-standing position, then plywood or a sheet of metal should be fastened to the back of the unit to ensure that chimney-effect cooling will be achieved. Larger free-standing variable frequency drives require minimum clearances around them for sufficient air flow to circulate through them, assuring adequate cooling.
Altitude affects the heat dissipation capability of the heat sink and units in locations at 3300 ft (1000 m) above sea level must be derated. A common rule of thumb is a 2% derating for every 1000 ft above the 3300 ft altitude level.
2) Supply line power quality: The line voltage (supply) to the VFD input should not vary plus or minus 10% because most VFDs will trip via a protective fault. This voltage stability should be considered when running conductors to the VFD and voltage drops should be calculated for long runs.
Very often external control signals are used to start/stop and control the speed of a variable frequency drive. Control signal types can vary depending on the application. It's not unusual to have a 115V or 24V control circuit for start commands and a 4-20mA or 0-5VDC signal for speed control. These control signals must be run independently of each other as well as separate from any power wiring. Induced noises can produce erratic VFD behavior that is very difficult to troubleshoot.
Tags: VFD installation
While there are many features associated with variable frequency drives (VFD), the following are the most important.
- Continuous run current rating. This is the maximum rms current the variable frequency drive can safely handle under all operating conditions at a fixed ambient temperature (usually 40 [degrees] C). Motor ball load sine wave currents must be equal to or less than this rating.
- Overload current rating. This is an inverse time/current rating that is the maximum current the variable frequency drive can produce for a given time frame. Typical ratings are 110% to 150% overcurrent for 1 min, depending on the manufacturer. Higher current ratings can be obtained by oversizing the variable frequency drive. This rating is very important when sizing the variable frequency drive for the currents needed by the motor for break-away torque.
- Line voltage. As with any motor controller, an operating voltage must be specified. Variable frequency drives are designed to operate at some nominal voltage such as 240VAC or 480VAC, with an allowable voltage variation of plus or minus 10%. Most motor starters will operate beyond this 10% variation, but variable frequency drives will not and will go into a protective trip. A recorded voltage reading of line power deviations is highly recommended for each application.
All said, in practice, an engineer ends up selecting a particular switching frequency for more subtle reasons. One reason would be because the application note or demo board of a particular control chip uses a particular frequency. Engineering product development involves designing and bringing to market the product as fast and with as less risk as possible. So reuse of circuits, topologies and associated switching frequency is common.
As a summary, one should choose a fs as low as possible. Our experience shows a fs between 20kHz and 50kHz is good for converters above 2kW but less than 60kW (or so). Upto 150kHz is good for off line converter with a power range of few watts to about 2kW. Anything above 200kHz should be used for lower wattage converter where isolation is not required.
As a summary, one should choose a fs as low as possible. Our experience shows a fs between 20kHz and 50kHz is good for converters above 2kW but less than 60kW (or so). Upto 150kHz is good for off line converter with a power range of few watts to about 2kW. Anything above 200kHz should be used for lower wattage converter where isolation is not required.
(1) As the low voltage VFD over-current of the control circuit cables is generally small, so the size of the control cable can be standardized, in order to avoid the interference caused by malfunction, the control cables should be twisted shielded wires;
(2) The control line and the main circuit cable laying
The VFD control lines should be laid separate from the main circuit cable and other power cable, and as far away as possible from the main circuit like more than 100mm; And don't parallel to the main circuit cable laying, do not cross the main circuit, if it must cross then it should be a vertical cross method.
(3) The cable shielding
The VFD cable shielding can adopt grounded metal tube or shielded cable. One end of Shielded layer connects to the VFD drive control circuit common (COM), but do not connect to the VFD ground end (e), the other end of the shield is vacant.
(4) The volume control switching line
The VFD switching control lines are allowed not to use the shielded wire, but two of the same signal lines must be twisted around each other, the twist pitch of the strands should be as small as possible, and the shielded layer connects to the ground terminal E of the VFD, the signal cable maximum length should not exceed 50m.
(5) Control circuit grounding
- the weak voltage/current loop wire connect to earth, and the grounding wire should not be used as the transmitted signal circuit;
- the wire's grounding should be in the VFD side, use a dedicated ground terminal and do not shared with other ground terminals.
(2) The control line and the main circuit cable laying
The VFD control lines should be laid separate from the main circuit cable and other power cable, and as far away as possible from the main circuit like more than 100mm; And don't parallel to the main circuit cable laying, do not cross the main circuit, if it must cross then it should be a vertical cross method.
(3) The cable shielding
The VFD cable shielding can adopt grounded metal tube or shielded cable. One end of Shielded layer connects to the VFD drive control circuit common (COM), but do not connect to the VFD ground end (e), the other end of the shield is vacant.
(4) The volume control switching line
The VFD switching control lines are allowed not to use the shielded wire, but two of the same signal lines must be twisted around each other, the twist pitch of the strands should be as small as possible, and the shielded layer connects to the ground terminal E of the VFD, the signal cable maximum length should not exceed 50m.
(5) Control circuit grounding
- the weak voltage/current loop wire connect to earth, and the grounding wire should not be used as the transmitted signal circuit;
- the wire's grounding should be in the VFD side, use a dedicated ground terminal and do not shared with other ground terminals.
Brake unit is short for VFD dedicated energy braking unit or regenerative energy unit, mainly use for controlling heavy mechanical load and the situation requires rapid braking speed, to adsorb the motor's regenerate electric energy by brake resistor or feed back to current.
Braking resistor is one types of RXHG resistors, it's been used in controlling motor brake in variable frequency drives mechanism, to convert the regenerated electric energy into thermal energy during braking process of the electric motors.
1. Protect VFDs
Due to inertia effect, it will produce lots regenerative electric energy in the motor's fast braking process. It will affect the DC control part of VFDs if those electric energy can't be consumed in time, it leads to fault of VFDs, even worse, the VFDs would be broken. Thanks to the brake resistor solves this problem well enough to protect electric motors away from regenerative energy damage.
2. Protect power supply lines
The brake resistor converts regenerated electric energy into thermal energy and absorbs it during braking process, so it won't feed back to the power supply lines and harm it, therefore to protect power supply in stable running state.
1. Protect VFDs
Due to inertia effect, it will produce lots regenerative electric energy in the motor's fast braking process. It will affect the DC control part of VFDs if those electric energy can't be consumed in time, it leads to fault of VFDs, even worse, the VFDs would be broken. Thanks to the brake resistor solves this problem well enough to protect electric motors away from regenerative energy damage.
2. Protect power supply lines
The brake resistor converts regenerated electric energy into thermal energy and absorbs it during braking process, so it won't feed back to the power supply lines and harm it, therefore to protect power supply in stable running state.
Featured Articles
Variable Frequency Drive Harmonics and ...
A discussion of the benefits of variable frequency drives often leads to a question regarding electrical harmonic distortion ...
Three phase inverters
In the variable frequency drive rectifier paper, it explains how to go from three phase alternating current voltage to a direct ...
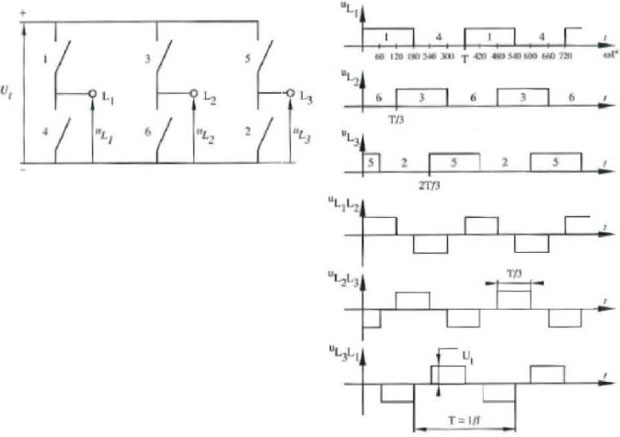
Variable frequency drive Advantages & ...
VFDs are good for variable speed, in a water pump this is used to maintain a steady pressure, they will smooth out variances in ...
Variable frequency drive Rectifier
To understand variable frequency drive (VFD) better, it's necessary to explain some of the main parts of the variable frequency ...
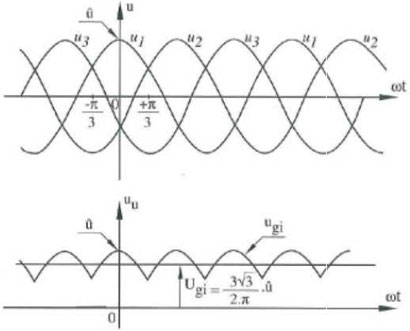
VFD controlled Induction motor ...
This paper presents a procedure to measure the efficiency on an induction motor fed by a VFD by the all operation range to speed ...
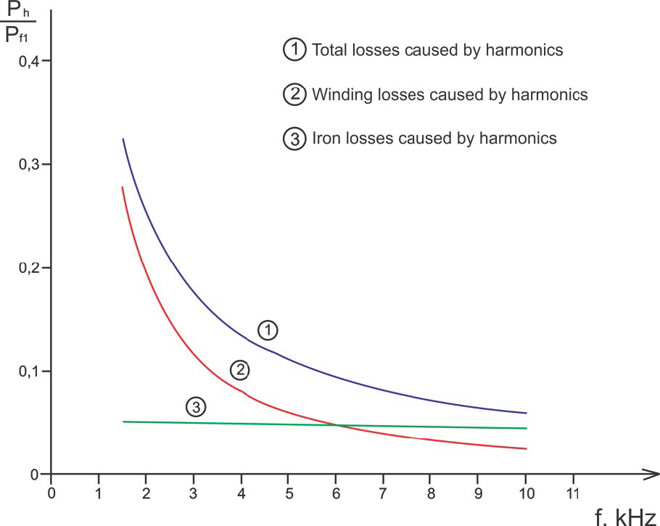
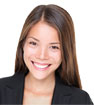
VFD manufacturers

