Home » Case study
Using a variable frequency drive (VFD) in co-operation with a pressure sensor, the supply fan can maintain a precise flow rate. Since the system does not modulate, the pressure downstream of the filter is proportional to flow. As the filter becomes dirty and its pressure drop increases, the VFD automatically increases the speed of the fan to compensate. In addition to allowing true constant air volume control, the VFD saves energy and provides a soft-start increasing the life expectancy of the filters.
We are working on a study related to Cooling Towers. We want to decrease cooling water supply temperature going to steam condenser to maintain vacuum inside it. One way is to increase capacity of cooling tower by installing another cooling tower cell. Other way is to keep the same cooling tower and install variable frequency drives (VFD) on cooling tower fans so that we can increase fan speed (hence increase air flow) to get the required cooling and reduced cooling water supply temperature.
It is therefore advisable to contact the designer or the supplier as the relative humidity in case of Cooling Towers is the controlling parameter, which in the case is 50%. So, if structural stability calculation from the supplier allows you, you may go for the option you have thought.
It is therefore advisable to contact the designer or the supplier as the relative humidity in case of Cooling Towers is the controlling parameter, which in the case is 50%. So, if structural stability calculation from the supplier allows you, you may go for the option you have thought.
I want to control a motor (pump) speed via variable frequency drive in such a way that when temperature of the water increases the pump speed also increased and when temperature of the water decreases the speed of the motor (pump) also decreased. Can we used external PID control with a variable frequency drive OR use a variable frequency drive having a PID control option and then tune up that PID control?
One option is to use a temperature sensor and a transmitter for temperature reading and use it directly for control in a variable frequency drive (VFD). Another option is to hook it up to a control system like DCS. You can use PID controller in DCS for control. The output from DCS can be given to the VFD.
One option is to use a temperature sensor and a transmitter for temperature reading and use it directly for control in a variable frequency drive (VFD). Another option is to hook it up to a control system like DCS. You can use PID controller in DCS for control. The output from DCS can be given to the VFD.
Furthermore, the system may transition between siphon and non-siphon conditions, particularly if the flow range is large. This could be a result of using multiple duty pumps and/or variable frequency drives.
If this is an existing system and you're having problems, there's a high probably that the static head hasn't been properly addressed during design. You may have unstable duty conditions and the pumps may operate anywhere from too far left of curve to too far right of curve. If the pipeline undulates and the HGL is close to pipe level, air may enter the pipeline at air release valves and create increased static head due to air pockets in the pipework.
If this is an existing system and you're having problems, there's a high probably that the static head hasn't been properly addressed during design. You may have unstable duty conditions and the pumps may operate anywhere from too far left of curve to too far right of curve. If the pipeline undulates and the HGL is close to pipe level, air may enter the pipeline at air release valves and create increased static head due to air pockets in the pipework.
This way you can break-down the selection and select pumps based on maximum efficiency in all 3 conditions. Obviously it seems sensible to use multiple pump systems and or a variable frequency drive - VFD driven system. For safety reasons we would always advise at least 2 pumps for such a system.
The type of pump to be selected cannot be properly be decided without the above info - it is however common to use surface pumps such as double suctions.
The type of pump to be selected cannot be properly be decided without the above info - it is however common to use surface pumps such as double suctions.
I have a multistage centrifugal pump in a test rig, and I need change the volume flow very often, although it does not to be accurate. I used to have a variable frequency drive (VFD), and can vary the flow rate very accurately. But the VFD made lots of troubles in the past, noise to the SCADA system, damage in transportation. So I am searching for a rough, simple alternative ways to change the volume. The globe valve option has been considered, but I am still looking for other alternative ways?
The motors three phase and squirrel cage only you can allow some starts per hour, for example a motor of 100HP@1800RPM only allow 2 start on cold and 10 on Hot per hour. However is possible to increase this condition using Soft Starter and Variable Frequency Drive (VFD). With soft starter you can obtain a 30% more in this allow starts, so you using VFD this trend to infinite.
Also you need review, if the brake of motors can inject energy to power network in this case you need brake resistor or using VFD with reinject the power to network.
Also you need review, if the brake of motors can inject energy to power network in this case you need brake resistor or using VFD with reinject the power to network.
We have commissioned a 220 KW variable frequency drive (VFD) at a customer in XYZ State. They have a 12 MW power plant are having Turbines & one steam boiler. For controlling of speed of FD fan you have used 220 KW, F7 model L&T Yaskawa VFD.
Earlier they were using for 220 KW soft starter for driving FD fan. On 25th Feb 2013, they have connected 220 KW VFD to achieve power saving. The power plant is paralleled with state XYZ Electric Board) grid. & they are exporting/Importing power to/from State grid.
Earlier they were using for 220 KW soft starter for driving FD fan. On 25th Feb 2013, they have connected 220 KW VFD to achieve power saving. The power plant is paralleled with state XYZ Electric Board) grid. & they are exporting/Importing power to/from State grid.
I have 6 injection molding machines. We use 10 hp motor for cooling, sometime 2-3 machine stop for repair. Can I use variable frequency drive for motor to save power, which pressure sensor I use to feedback to VFD input?
Your application is a very good candidate for using VFD. It can save good amount of power and in your case the payback period can be as low as 1 year or so depending upon your reduced cooling water requirement. The more you run the motor, at lower speed, more the saving. As per affinity law the power required by a motor running at 1/2 speed is only 1/8 of original power. For example a 7.5 KW motor consumes only approx 1 kw when running at half speed. Of course the pump out put in volumetric terms also will reduce correspondingly.
Your application is a very good candidate for using VFD. It can save good amount of power and in your case the payback period can be as low as 1 year or so depending upon your reduced cooling water requirement. The more you run the motor, at lower speed, more the saving. As per affinity law the power required by a motor running at 1/2 speed is only 1/8 of original power. For example a 7.5 KW motor consumes only approx 1 kw when running at half speed. Of course the pump out put in volumetric terms also will reduce correspondingly.
Refrigeration compressors, air compressors or gas compressors? Irrespective of which type, the best solution is to have 3 individual variable frequency drive (VFD) running the compressor. These can be started in sequence to minimize power surge. A more economical solution would be to use a single VFD for startup and modulation of a compressor. When this compressor runs to full speed, a bypass contactor kicks in and the VFD can be switched over to a second compressor and then the 3rd when all compressors are running. For added reliability, it may be possible to add a standby VFD. I don't see any advantage of using a single large variable frequency drive for 3 compressors other than the need to synchronize them.
This article have a study of the wireless group control system with variable frequency drive (VFD) applied in a Chinese plantation irrigation system. China is a fresh water resources scarce country, agricultural irrigation occupies a large part of the water resources. Because long-term use of traditional farming patterns, low utilization rate of irrigation water, irrigation water wasted is a very serious problem in China. In order to improve the irrigation efficiency and save the water resource, based on an example of a large plantation in Shandong Province of China, this study designs a wireless group control system with variable frequency drive according to the specific situation of the irrigation wells dispersed. It realizes the communication between the main control room and 13 dispersed wells through wireless network. In the distributed sub-stations, we use the VFD to drive the lift pump to achieve the precise allocation of irrigation water, the saving effect is significant. Besides, the article especially introduces the software realization of the wireless communication.
Notes that for the combinations where we had the same number of opened records, the power suffers no change, but when it is used the VFD; there is a variation of the power consumed. It is observed that with the variable frequency drive, the consumption is reduced when have lower energy losses, i.e. when the opened records are closer to the irrigation pump, it can be checked by observing Figure 1. The lower energy consumption for both systems was in the combination 13, which also provided the largest difference in energy consumption, being 40% lower for the use of a VFD.
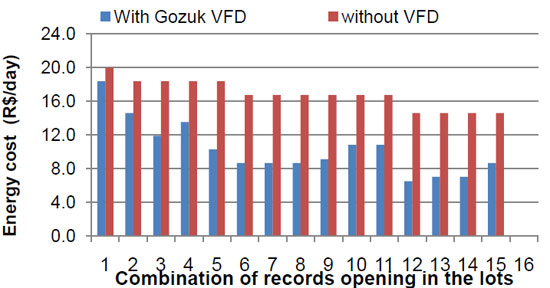
After evaluation of the irrigation pumping system in the laboratory, there was a reduction in the cost of electricity for pumping in irrigated districts applying different levels of automation when using the VFD.
The use of the VFD demonstrated to be an effective tool in reducing the cost of electricity in irrigation pumping system for irrigated districts, in the case study, its use represented 40% of energy savings by VFDs.
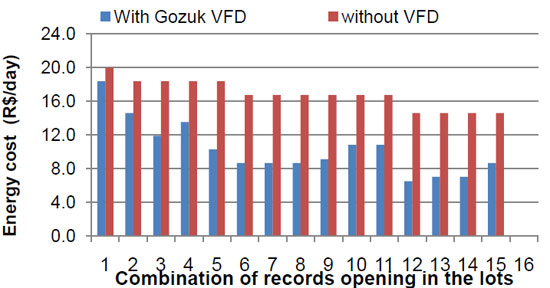
After evaluation of the irrigation pumping system in the laboratory, there was a reduction in the cost of electricity for pumping in irrigated districts applying different levels of automation when using the VFD.
The use of the VFD demonstrated to be an effective tool in reducing the cost of electricity in irrigation pumping system for irrigated districts, in the case study, its use represented 40% of energy savings by VFDs.
Featured Articles
Variable frequency drive on Cooling ...
We are working on a study related to Cooling Towers. We want to decrease cooling water supply temperature going to steam ...
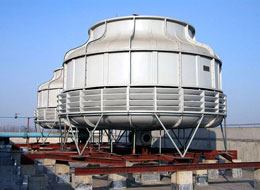
VFD in China plantation irrigation ...
This article have a study of the wireless group control system with variable frequency drive (VFD) applied in a Chinese ...
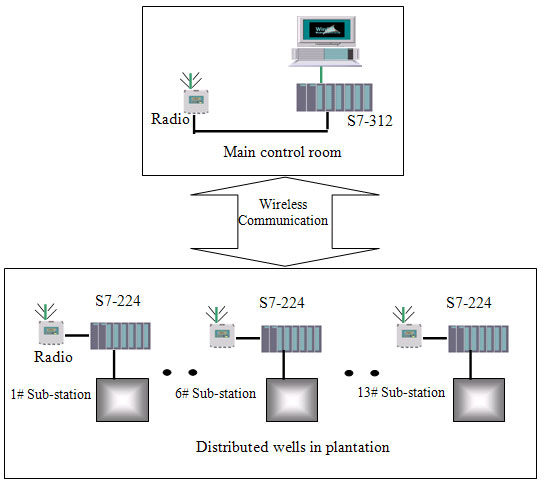
Variable frequency drive energy ...
Notes that for the combinations where we had the same number of opened records, the power suffers no change, but when it is used ...
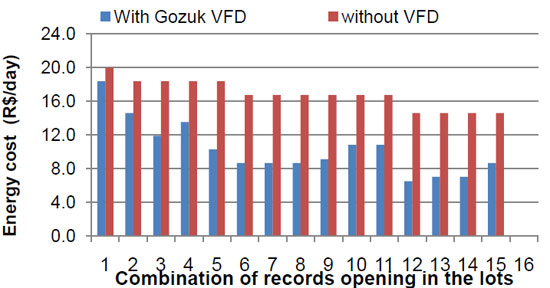
VFD for pumps in variable flow water ...
Variable flow water system has played an important role in the field of energy saving with the VFD widely used in practical ...
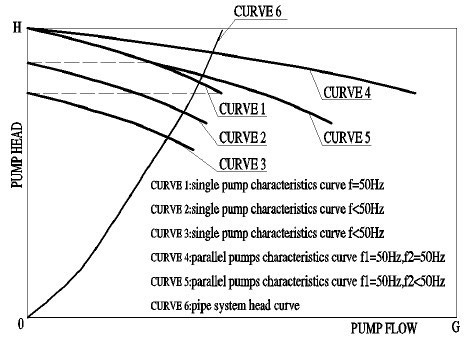
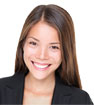
VFD manufacturers

