What is Dynamic Braking in variable frequency drive?
An uncontrolled method of braking. After power is removed from a dc motor armature (assuming the field supply is maintained), the motor acts as a generator and turns the kinetic energy of the rotating motor and load into electrical energy. This is dissipated as heat in a resistor. A normally closed contact on the motor starter connects the motor armature circuit to the resistor.
The above describes dynamic braking (DB) in its pure sense, and is frequently used with dc thyristor variable frequency drives.
However, with the newer variable frequency drive that has a dc bus, dynamic braking is also used to describe a braking method for variable frequency drives that dissipate the energy in a resistor connected across the dc bus.
No form of dynamic braking operates as a holding brake. Holding must be accomplished with a mechanical brake. The dynamic braking resistor is a dumping ground for the energy contained in the rotating system, allowing it to be "bled off" as electrical energy. Because the operational mode has changed from motoring (power flow from VFD source to machine) to generating (from rotating machine to VFD), the variable frequency drive must be capable of supplying power in both directions.
Dynamic performance: The ability of a VFD to respond to a change in command. Typically measured in radians/sec when the motor is included, the higher the number, the faster the variable frequency drive can respond. For many applications, a response of 1 to 5 rad/sec is sufficient. High-performance servo applications require response in the hundreds of rad/sec. When the response of only the VFD controller is indicated, the response may be indicated in rad/sec or in Hertz (Hz).
The above describes dynamic braking (DB) in its pure sense, and is frequently used with dc thyristor variable frequency drives.
However, with the newer variable frequency drive that has a dc bus, dynamic braking is also used to describe a braking method for variable frequency drives that dissipate the energy in a resistor connected across the dc bus.
No form of dynamic braking operates as a holding brake. Holding must be accomplished with a mechanical brake. The dynamic braking resistor is a dumping ground for the energy contained in the rotating system, allowing it to be "bled off" as electrical energy. Because the operational mode has changed from motoring (power flow from VFD source to machine) to generating (from rotating machine to VFD), the variable frequency drive must be capable of supplying power in both directions.
Dynamic performance: The ability of a VFD to respond to a change in command. Typically measured in radians/sec when the motor is included, the higher the number, the faster the variable frequency drive can respond. For many applications, a response of 1 to 5 rad/sec is sufficient. High-performance servo applications require response in the hundreds of rad/sec. When the response of only the VFD controller is indicated, the response may be indicated in rad/sec or in Hertz (Hz).
Post a Comment:
You may also like:
Featured Articles
Non-Enclosure Variable Frequency Drive ...
No enclosure (cover), reducing installation space and cost effective. Widely used in All-In-One control cabinet. Keep the same ...
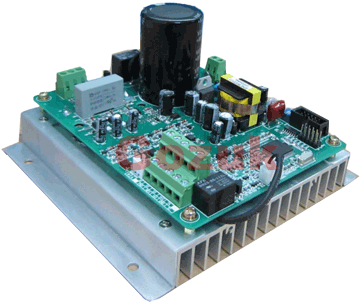
Variable frequency drive application ...
Variable Frequency Drive (VFD) can be used in lots of fields. Variable frequency drives are widely used to control the speed of ...
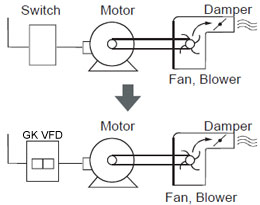
Variable frequency drive in HVAC ...
Variable frequency drives (VFD) have been used for HVAC systems in buildings for more than 40 years. But only in recent years, ...
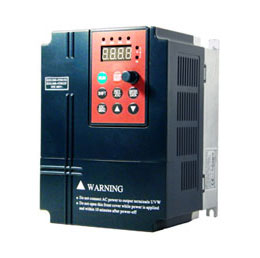
Variable Frequency Drive Harmonics and ...
A discussion of the benefits of variable frequency drives often leads to a question regarding electrical harmonic distortion ...
Three phase inverters
In the variable frequency drive rectifier paper, it explains how to go from three phase alternating current voltage to a direct ...
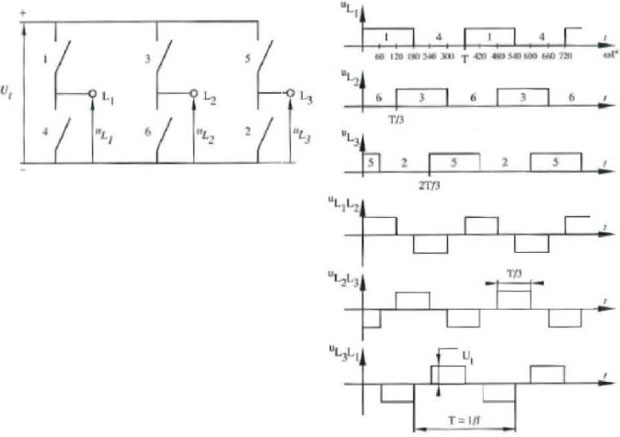
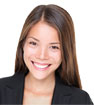
VFD manufacturers

