VFD with PLC for motor controls
The two most important emerging technologies associated with motor control are variable frequency drives & programmable logic controllers. VFDs allow motor driven loads to operate within a wide range of speeds. Con trolling motor speeds to load requirements can increase both the efficiency & performance of a motor installation. A programmable logic controller (PLC) is a type of computer commonly used in motor control applications. The traditional motor control circuit is hard-wired while PLC control is program-based. This section deals with the unique installation requirements of these electronic control systems.
The primary function of any electronic VFD is to control the speed, torque, acceleration, deceleration, & direction of rotation of a machine. Unlike constant speed systems, the VFD permits the selection of an infinite number of speeds within its operating range.
The use of VFDs in pump & fan systems can greatly increase their efficiency. Outdated technology most often used throttles or dampers to interrupt the flow as a means to control it. The fluid or air was held back by the throttle or damper but the energy used to move the fluid or air was then dissipated uselessly. That wasted energy was still accounted for & paid for. Running a system this way is like driving a car with the accelerator pressed to the floor while con trolling speed with the brake. An electronic VFD, on the other hand, allows precise control of motor output. In the case of centrifugal fans & pumps, there is a significant savings in the power required to handle the load.
The primary function of any electronic VFD is to control the speed, torque, acceleration, deceleration, & direction of rotation of a machine. Unlike constant speed systems, the VFD permits the selection of an infinite number of speeds within its operating range.
The use of VFDs in pump & fan systems can greatly increase their efficiency. Outdated technology most often used throttles or dampers to interrupt the flow as a means to control it. The fluid or air was held back by the throttle or damper but the energy used to move the fluid or air was then dissipated uselessly. That wasted energy was still accounted for & paid for. Running a system this way is like driving a car with the accelerator pressed to the floor while con trolling speed with the brake. An electronic VFD, on the other hand, allows precise control of motor output. In the case of centrifugal fans & pumps, there is a significant savings in the power required to handle the load.
Post a Comment:
You may also like:
Featured Articles
What is VFD, How it works? - VFD ...
VFD is shorted for Variable Frequency Drive (also known as AC Drives and Inverters) -- that's used to make an AC motor working in ...
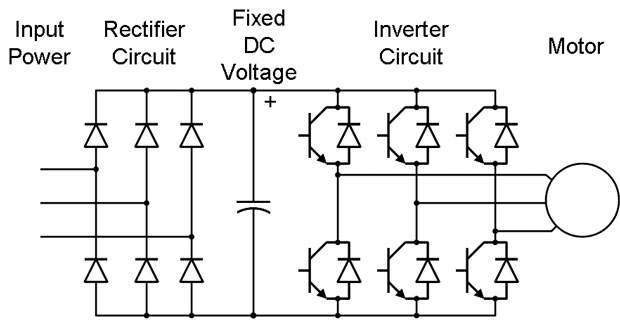
VFD: Insulated Gate Bipolar Transistor ...
IGBT (insulated gate bipolar transistor) provides a high switching speed necessary for PWM VFD operation. IGBTs are capable of ...
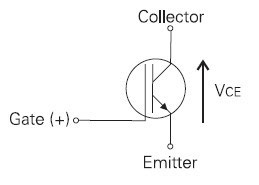
Three phase inverters
In the variable frequency drive rectifier paper, it explains how to go from three phase alternating current voltage to a direct ...
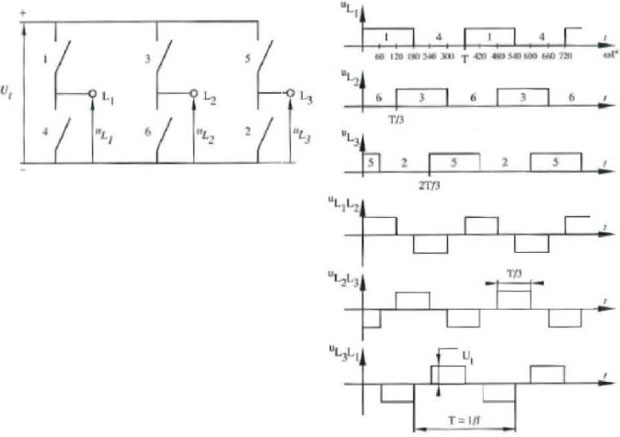
Variable frequency drive Rectifier
To understand variable frequency drive (VFD) better, it's necessary to explain some of the main parts of the variable frequency ...
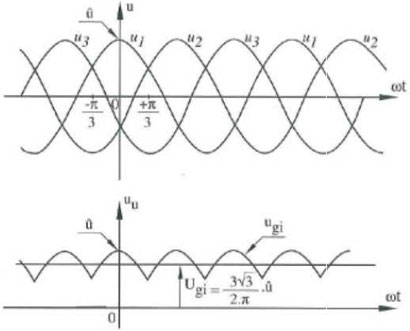
Variable Frequency Drive Harmonics and ...
A discussion of the benefits of variable frequency drives often leads to a question regarding electrical harmonic distortion ...
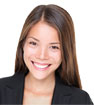
VFD manufacturers

