Variable frequency drive Tension Control
(The term, variable frequency drive, also refer to AC drive, frequency inverter, adjustable speed drive)
There are two ways in tension control, one way is to control the output torque of the motor, the other way is to control the motor speed. Variable frequency drive (VFD) open-loop control mode is complied with the first way, which doesn't need tension feedback. The term, "open-loop", means there is no tension feedback signal to the VFD, the VFD control the output frequency or torque to achieve the control purpose, and with no relation whether there is an encoder or not. Torque control mode means the VFD controls the motor torque instead of the frequency, the output frequency is automatically changed according to the speed.

Fig. 1 Open loop tension control
According to the formula
Variable frequency drive can control the motor output torque precisely in closed loop vector control mode, in such control mode, the VFD must install encoder (VFD with PG card). Close loop tension control mode adds tension feedback regulator on the basic of open loop. Using tension feedback signal and tension setting value to form PID closed loop control, to adjust the VFD output torque command, thereby achieve higher precision tension control.
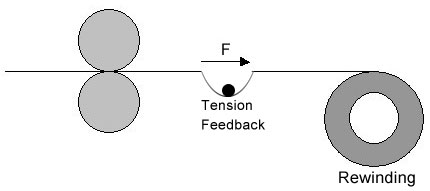
Fig. 2 Closed loop tension control
Standard tension control algorithms are available in most VFDs from ABB/ Siemens/ Gozuk and so on. They have inbuilt blocks suiting to Digital Radius computation type/ Line speed follower - diameter feedback type/ Line follower tension trim/ Line follower dancing roller position trim etc. and many more configurations. It is the material and the process to be adapted in the machine along with final output requirements will decide the configuration to be selected and mechanicals to be adapted and finally control blocks to be configured and tuned. They also have dedicated control loops for center wind or surface wind depending upon application.
Typical applications of tension control VFD: Wire and cable, optical fiber cable, paper processing, printing and dyeing, textile, leather, metal foil processing, etc.
There are two ways in tension control, one way is to control the output torque of the motor, the other way is to control the motor speed. Variable frequency drive (VFD) open-loop control mode is complied with the first way, which doesn't need tension feedback. The term, "open-loop", means there is no tension feedback signal to the VFD, the VFD control the output frequency or torque to achieve the control purpose, and with no relation whether there is an encoder or not. Torque control mode means the VFD controls the motor torque instead of the frequency, the output frequency is automatically changed according to the speed.

Fig. 1 Open loop tension control
According to the formula
F = T / RWhere F is the material tension, T is the rewind shaft torque, R is the radius of rewind, which we can know, we can control the material tension if the torque of the rewind shaft changes according to the roll diameter changes, which is the basic of open-loop tension control mode.
Variable frequency drive can control the motor output torque precisely in closed loop vector control mode, in such control mode, the VFD must install encoder (VFD with PG card). Close loop tension control mode adds tension feedback regulator on the basic of open loop. Using tension feedback signal and tension setting value to form PID closed loop control, to adjust the VFD output torque command, thereby achieve higher precision tension control.
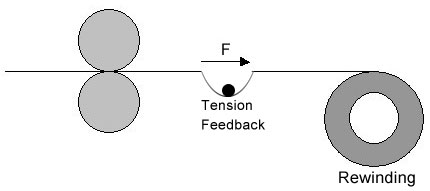
Fig. 2 Closed loop tension control
Standard tension control algorithms are available in most VFDs from ABB/ Siemens/ Gozuk and so on. They have inbuilt blocks suiting to Digital Radius computation type/ Line speed follower - diameter feedback type/ Line follower tension trim/ Line follower dancing roller position trim etc. and many more configurations. It is the material and the process to be adapted in the machine along with final output requirements will decide the configuration to be selected and mechanicals to be adapted and finally control blocks to be configured and tuned. They also have dedicated control loops for center wind or surface wind depending upon application.
Typical applications of tension control VFD: Wire and cable, optical fiber cable, paper processing, printing and dyeing, textile, leather, metal foil processing, etc.
Post a Comment:
You may also like:
Featured Articles
Variable frequency drive Rectifier
To understand variable frequency drive (VFD) better, it's necessary to explain some of the main parts of the variable frequency ...
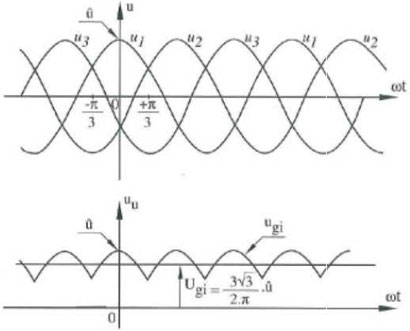
What is VFD, How it works? - VFD ...
VFD is shorted for Variable Frequency Drive (also known as AC Drives and Inverters) -- that's used to make an AC motor working in ...
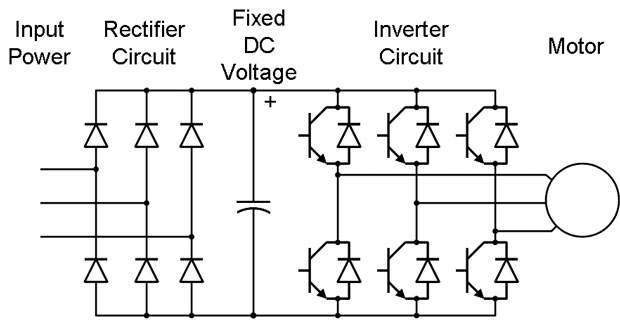
VFD controlled Induction motor ...
This paper presents a procedure to measure the efficiency on an induction motor fed by a VFD by the all operation range to speed ...
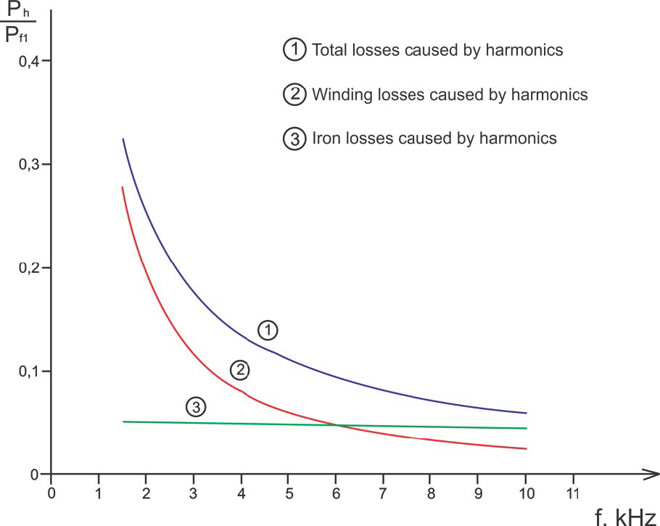
VFD: Insulated Gate Bipolar Transistor ...
IGBT (insulated gate bipolar transistor) provides a high switching speed necessary for PWM VFD operation. IGBTs are capable of ...
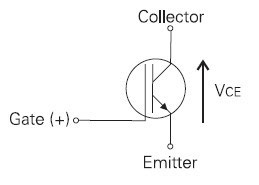
Three phase inverters
In the variable frequency drive rectifier paper, it explains how to go from three phase alternating current voltage to a direct ...
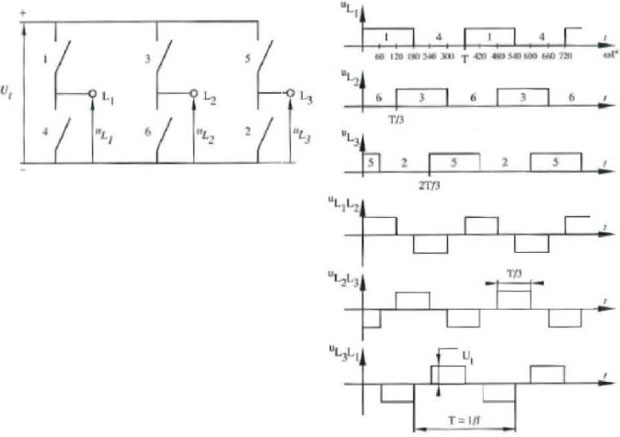
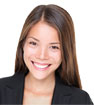
VFD manufacturers

