Home » Applications » VFD selection for refrigeration compressor
VFD selection for refrigeration compressor
Choose a variable frequency drive (VFD) for refrigeration compressor control must be conducted with great care, as a variable frequency drive selected too small-sized may present some disadvantages. These can be avoided by using the VFD selection software. Based on a process of individual selection and qualifying of the variable frequency drive suited for a given refrigeration compressor, safe and energy-saving operation of the refrigeration compressor can be achieved.
Experiences made in over 10,000 VFD installations in refrigeration and A/C projects have led to a list of priorities for the correct selection of a suitable variable frequency drive.
List of priorities for variable frequency drive selection
(1) The refrigeration compressor motor winding must not be overheated. This happens when the starting torque of a variable frequency drive dimensioned too small is not sufficient for starting the refrigeration compressor. The consequence of a stalled start is insufficient cooling of the refrigeration compressor motor. The winding temperature will then rise quickly and at 120 °C or above it is in danger (see the Figure on right).
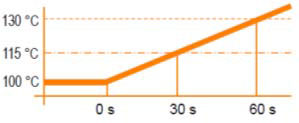
(2) A stalled starting attempt has to be detected immediately and the variable frequency drive inhibited before the winding temperature increases to a critical temperature. Restarting of the variable frequency drive must be prevented for a period of at least 1 minute.
(3) With the starting current available, the highest possible starting torque must be achieved. The higher the starting torque, the safer is starting. With the same current, the starting torque of the variable frequency drives presented hereafter is 20 % higher than that of a conventional VFD intended for industrial use.
(4) Provided the refrigeration compressor motor is selected correctly with an appropriate reserve in motor size, the maximum frequency of the refrigeration compressor can be increased to the mechanical limits until the maximum motor current is reached. This enables a high so-called Control Factor can be reached. The Control Factor is defined as follows:
Motor-current based variable frequency drive selection
The Technical Information describes a method for the safe selection of VFD, based on the following data given:
New method of VFD selection
By means of the new selection software, several new factors and criteria are considered in addition to dimensioning on the basis of motor-current alone:
(7) Refrigeration compressor start scenario – establishing worst-case start-up conditions. A refrigeration compressor start at a high ambient temperature after a long-term power-failure (>= 15 minutes) is considered as the most difficult starting condition. In accordance with the information provided in the software of most refrigeration compressor manufacturers the following starting points will be used:
(9) Consideration of refrigeration compressor make and type. With reciprocating compressors the number of cylinders is particularly important (see following figure). The starting torque of a 2-cylinder compressor e.g. is twice as high as the average torque.
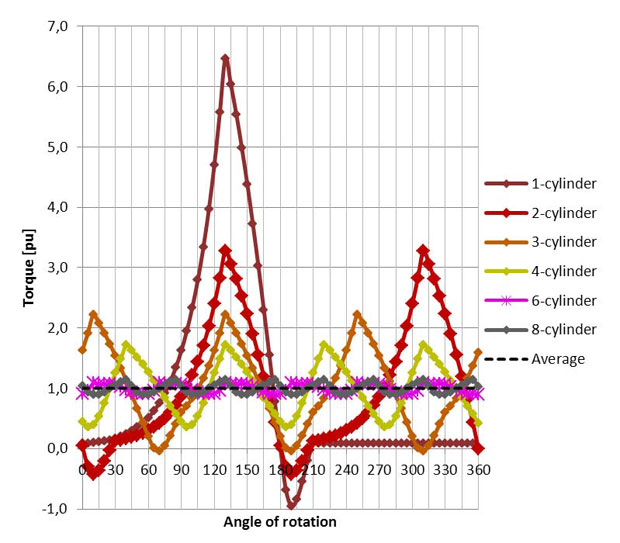
(10) Consideration of rack-assisted starting. With an intelligent control system, fixed-speed compressors are started first. As soon as suction pressure is close to the setpoint, the VFD-controlled compressors are activated.
(11) Calculating the starting current required.
(12) Selection of the smallest possible variable frequency drive able to supply the starting current needed.
For manual selection, a consideration of all above factors described above would be too complicated. Detailed VFD and refrigeration compressor information stored in a data base accessed by a selection software is necessary.
The following data are required to select a suitable refrigeration variable frequency drive:
In many cases information on electrical switchgear is included in the variable frequency drive manufacturers technical documentation. However, switches and cables are usually over dimensioned, as variable frequency drive operating data are not suitable for the selection of switches and cables in refrigeration applications.
Sometimes too much copper is used. It is more economical to select electrical switchgear on the basis of the refrigeration compressor's electrical operating data.
Conclusions
With the exact selection of refrigeration variable frequency drives and electrical controls and equipment is made possible. The equipment suggested is often more economical than that chosen with conventional methods.
Experiences made in over 10,000 VFD installations in refrigeration and A/C projects have led to a list of priorities for the correct selection of a suitable variable frequency drive.
List of priorities for variable frequency drive selection
(1) The refrigeration compressor motor winding must not be overheated. This happens when the starting torque of a variable frequency drive dimensioned too small is not sufficient for starting the refrigeration compressor. The consequence of a stalled start is insufficient cooling of the refrigeration compressor motor. The winding temperature will then rise quickly and at 120 °C or above it is in danger (see the Figure on right).
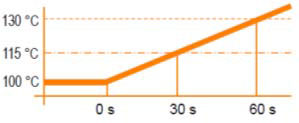
(2) A stalled starting attempt has to be detected immediately and the variable frequency drive inhibited before the winding temperature increases to a critical temperature. Restarting of the variable frequency drive must be prevented for a period of at least 1 minute.
(3) With the starting current available, the highest possible starting torque must be achieved. The higher the starting torque, the safer is starting. With the same current, the starting torque of the variable frequency drives presented hereafter is 20 % higher than that of a conventional VFD intended for industrial use.
(4) Provided the refrigeration compressor motor is selected correctly with an appropriate reserve in motor size, the maximum frequency of the refrigeration compressor can be increased to the mechanical limits until the maximum motor current is reached. This enables a high so-called Control Factor can be reached. The Control Factor is defined as follows:
Control Factor CF = Variation of Variable-speed Compressor refrigeration power / Fixed-speed Compressor step(5) Achieving the highest possible Control Factor is important for the following reasons:
- A good Control Factor results in a good control of suction pressure. The suction pressure is stable and the expansion valve can operate well with a high efficiency (i.e. energy saving), resulting in optimum filling of the evaporator.
- The reduced number of starts of the Fixed-speed compressors in a refrigeration compressor rack leads to an extended working life of the refrigeration system
- Maximum rack refrigeration power is relatively high.
Motor-current based variable frequency drive selection
The Technical Information describes a method for the safe selection of VFD, based on the following data given:
- Maximum motor current, as stated in the refrigeration compressor manufacturer's documentation.
- Factor considering the number of cylinders with reciprocating compressors
- Factors relevant for screw and scroll compressor units
- Use of conventional industrial variable frequency drives
New method of VFD selection
By means of the new selection software, several new factors and criteria are considered in addition to dimensioning on the basis of motor-current alone:
(7) Refrigeration compressor start scenario – establishing worst-case start-up conditions. A refrigeration compressor start at a high ambient temperature after a long-term power-failure (>= 15 minutes) is considered as the most difficult starting condition. In accordance with the information provided in the software of most refrigeration compressor manufacturers the following starting points will be used:
- Evaporating temperature: …10 °C (depending on the refrigerant used)
- Condensing temperature: corresponding to the ambient temperature, e.g. 43 °C in summer
(9) Consideration of refrigeration compressor make and type. With reciprocating compressors the number of cylinders is particularly important (see following figure). The starting torque of a 2-cylinder compressor e.g. is twice as high as the average torque.
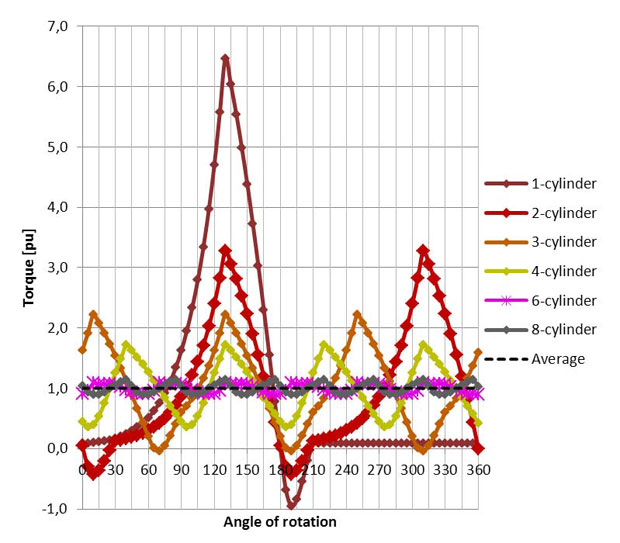
(10) Consideration of rack-assisted starting. With an intelligent control system, fixed-speed compressors are started first. As soon as suction pressure is close to the setpoint, the VFD-controlled compressors are activated.
(11) Calculating the starting current required.
(12) Selection of the smallest possible variable frequency drive able to supply the starting current needed.
For manual selection, a consideration of all above factors described above would be too complicated. Detailed VFD and refrigeration compressor information stored in a data base accessed by a selection software is necessary.
The following data are required to select a suitable refrigeration variable frequency drive:
- Compressor manufacturer: Bitzer, Bock, Dorin, DWM-Copeland, etc.
- Refrigerant: currently R 404A / R 507, R 134a, R 22, R 407C, R 410A, R 717, R 744_SC/TC
- Compressor type: currently reciprocating, screw and scroll (semi-hermetic, hermetic or open)
- Compressor selection list including all relevant electrical and refrigeration data.
- Electrical supply voltage (380 V pre-selected)
- Motor connection: Star, delta, part winding
- Starting torque factor: Taking into account starting conditions such as the maximum ambient temperature and/or rack-assisted starting
In many cases information on electrical switchgear is included in the variable frequency drive manufacturers technical documentation. However, switches and cables are usually over dimensioned, as variable frequency drive operating data are not suitable for the selection of switches and cables in refrigeration applications.
Sometimes too much copper is used. It is more economical to select electrical switchgear on the basis of the refrigeration compressor's electrical operating data.
Conclusions
With the exact selection of refrigeration variable frequency drives and electrical controls and equipment is made possible. The equipment suggested is often more economical than that chosen with conventional methods.
TRYING TO GET UO WITH SOME TO HELP ME ON YOUR DRIVE PRODUCTS IM IN THE USA
We have required for our ammonia compressor KC-6 VFD 110kw capacity. Please suggest.
Post a Comment:
You may also like:
Featured Articles
Variable frequency drive application ...
Variable Frequency Drive (VFD) can be used in lots of fields. Variable frequency drives are widely used to control the speed of ...
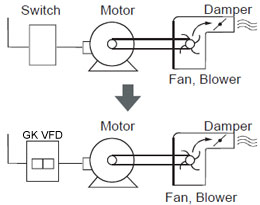
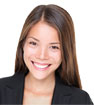
VFD manufacturers

