Home » Applications » VFD energy saving for Fans
VFD energy saving for Fans
Energy Savings
Air handling equipment consumes enormous quantities of energy, and deserves some thoughtful consideration by those who manage profits and, therefore, desire to save more money through energy management. The purpose of this cost justification guide is to provide a practical tool for management so that an estimate of VFD annual savings can be made. Unlike a computer generated payback analysis, this guide allows the user to see where the numbers come from and how the VFD stacks up against other flow control methods.
Methods of Flow Control
An air handling system will be engineered for 100% design flow, but many times could operate with less flow. Let's say that 50% flow is required sometime. What are the options? See Figure 1.
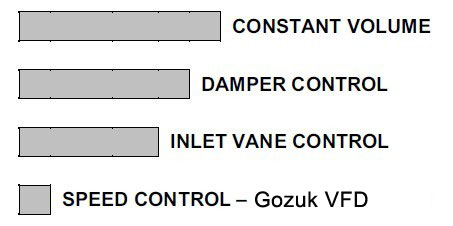
Some observations about these methods:
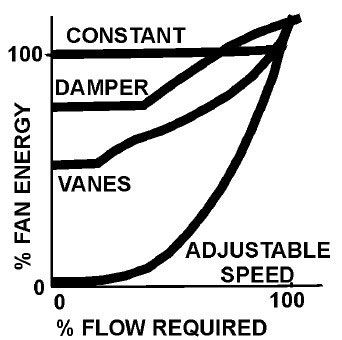
Calculating Payback
When the cost of VFD installation must be justified through energy savings, there are several pieces of information required. The most obvious are:
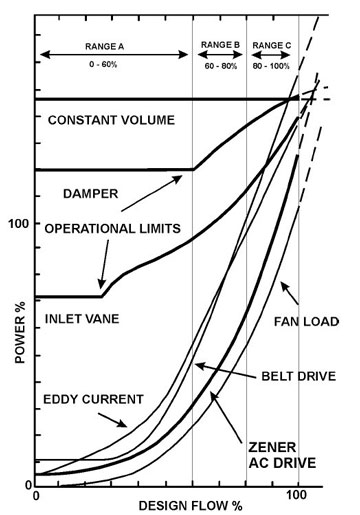
Additional Cost Justification
Energy savings alone may justify the installation of a VFD, however, there are even more savings to be realized through:
You Have Made The Best Decision
Variable frequency is the best method of flow control and the VFD motor speed control will give you superior performance. Why?
The savings index is calculated number based on savings hours per year and is derived from the curves in Figure 3. Theses are typical power vs. flow curves that are based on the % power required by a fan to produce design flow i.e. 100% design flow requires 100% power at the fan input shaft. These curves, and the savings index are based on a fan which is 10% oversized. Fans are usually oversized because:
The savings, in % power, between the VFD curve and, for instance, the damper control curve, were measured at 0, 60, 80 and 100% flow. This allowed calculation of an average saving figure in each flow range, which could be multiplied by the number of hours per year in that flow range.
Air handling equipment consumes enormous quantities of energy, and deserves some thoughtful consideration by those who manage profits and, therefore, desire to save more money through energy management. The purpose of this cost justification guide is to provide a practical tool for management so that an estimate of VFD annual savings can be made. Unlike a computer generated payback analysis, this guide allows the user to see where the numbers come from and how the VFD stacks up against other flow control methods.
Methods of Flow Control
An air handling system will be engineered for 100% design flow, but many times could operate with less flow. Let's say that 50% flow is required sometime. What are the options? See Figure 1.
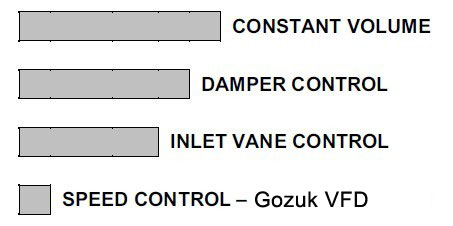
Some observations about these methods:
- Constant volume wastes energy.
- Dampers may be noisy and have limited turn down.
- Inlet vanes restrict flow even when wide open.
- The VFD has the ability to realize the fan to exact needs through speed control. The VFD also reduces fan noise while at the same time saving the most energy. Does this justify the extra cost?
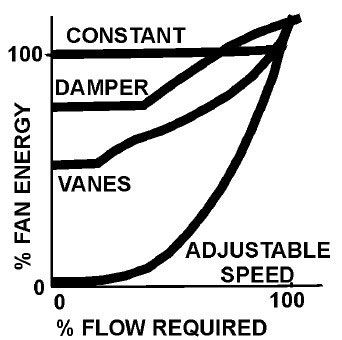
Calculating Payback
When the cost of VFD installation must be justified through energy savings, there are several pieces of information required. The most obvious are:
- Fan HP (not motor HP)
- Cost of electricity (including demand and power factor penalties).
- Cost of VFD installation.
- Hours/year from 0 – 60% flow – Range A.
- Hours/year from 60 – 80% flow – Range B.
- Hours/year from 80 – 100 % - flow – Range C.
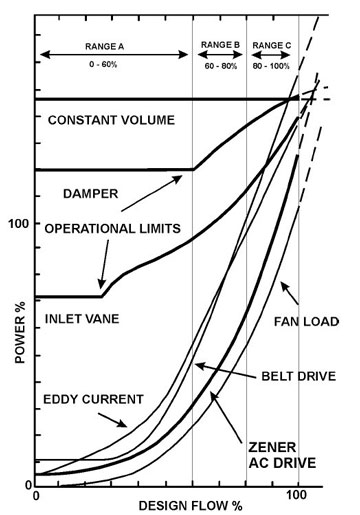
Additional Cost Justification
Energy savings alone may justify the installation of a VFD, however, there are even more savings to be realized through:
- Reduced mechanical wear and associated maintenance.
- Reduced power "demand charge" because the motor is started softly with no inrush current.
- Improved power factor.
- Probable reduction in the amount of air that must be conditioned (cooled, heated, dehumidified, etc.)
You Have Made The Best Decision
Variable frequency is the best method of flow control and the VFD motor speed control will give you superior performance. Why?
- Lowest power consumption
- Lowest installed cost.
- Least maintenance (saves wear and tear on the fan too).
- No inrush current (starting).
- Highest (near unity) power factor.
- Local sales, service, and application specialists.
The savings index is calculated number based on savings hours per year and is derived from the curves in Figure 3. Theses are typical power vs. flow curves that are based on the % power required by a fan to produce design flow i.e. 100% design flow requires 100% power at the fan input shaft. These curves, and the savings index are based on a fan which is 10% oversized. Fans are usually oversized because:
- filters clog and leaks develop
- design engineers are conservative
- the next smaller fan could not meet the design flow requirements
The savings, in % power, between the VFD curve and, for instance, the damper control curve, were measured at 0, 60, 80 and 100% flow. This allowed calculation of an average saving figure in each flow range, which could be multiplied by the number of hours per year in that flow range.
Post a Comment:
You may also like:
Featured Articles
Variable frequency drive application ...
Variable Frequency Drive (VFD) can be used in lots of fields. Variable frequency drives are widely used to control the speed of ...
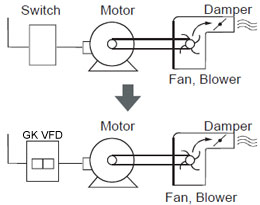
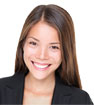
VFD manufacturers


May i know how to calculate the savings when operating a ID fan with damper control and with a VFD..?
And also FAn driven with fluid coupling with respect to a vfd..?