Variable frequency drive Direct Torque Control (DTC)
There are 3 types of control schemes for variable frequency drives, V/F control, Vector control and Flux control. Most major VFD manufacturers like ABB, Gozuk, Rockwell Automation, all have each technology. V/F is the oldest, most basic control scheme but is still used by all VFD manufactures for multiple motor applications. Vector technology offers enhanced control and the ability to control a motor closer to 0 speed (V/F is limited to 5 Hz as a minimum usually). Flux control is the highest level and can match DC performance such as full torque at 0 speed. Many VFD manufacturers have flux capability like Gozuk and ABB. ABB's version of flux control is Direct Torque Control (DTC).
DTC is a replacement of motor + gear. Usually it has high torque and low speed (and many pole pairs). I make a much clearer conclusion here by everyone's help:
1. The major advantage of DTC is fast torque response. The major disadvantage of DTC is the large current harmonic or torque ripple of the original algorithm. That also indicates the reason that why in the research area people keep working on improving algorithms or those estimators to reduce torque ripple even in the recent APEC 2014. Also, this can be proved by the improvements to DTC patents. However, due to these improvements, the DTC used in ABB variable frequency drive is as good as Field Oriented Control (FOC). This explains why people use DTC don't think the torque ripple is high.
2. The DTC is used only in ABB drives because of the patent issue. What I'm not sure is that it is because ABB extends the original patent or because of the patented improvements or even because of both.
Flux control is seldom needed by the load perhaps 5% of applications require this level of performance. ABB's Direct Torque Control can hit this higher level of performance as Gozuk VFD with its type of flux control. Manufacturers vary as to the use of flux control. Most manufacturers tend to only use the more complex flux control when the load requires this level of control. Other manufacturers, like ABB's DTC, tend to offer this level of control as standard on many more VFDs.
I'm working on flux weakening control of PMSM now and one of my friends works on DTC. Lately I may spend some time go through Direct Torque Control.
DTC is a replacement of motor + gear. Usually it has high torque and low speed (and many pole pairs). I make a much clearer conclusion here by everyone's help:
1. The major advantage of DTC is fast torque response. The major disadvantage of DTC is the large current harmonic or torque ripple of the original algorithm. That also indicates the reason that why in the research area people keep working on improving algorithms or those estimators to reduce torque ripple even in the recent APEC 2014. Also, this can be proved by the improvements to DTC patents. However, due to these improvements, the DTC used in ABB variable frequency drive is as good as Field Oriented Control (FOC). This explains why people use DTC don't think the torque ripple is high.
2. The DTC is used only in ABB drives because of the patent issue. What I'm not sure is that it is because ABB extends the original patent or because of the patented improvements or even because of both.
Flux control is seldom needed by the load perhaps 5% of applications require this level of performance. ABB's Direct Torque Control can hit this higher level of performance as Gozuk VFD with its type of flux control. Manufacturers vary as to the use of flux control. Most manufacturers tend to only use the more complex flux control when the load requires this level of control. Other manufacturers, like ABB's DTC, tend to offer this level of control as standard on many more VFDs.
I'm working on flux weakening control of PMSM now and one of my friends works on DTC. Lately I may spend some time go through Direct Torque Control.
Post a Comment:
You may also like:
Featured Articles
Variable frequency drive Rectifier
To understand variable frequency drive (VFD) better, it's necessary to explain some of the main parts of the variable frequency ...
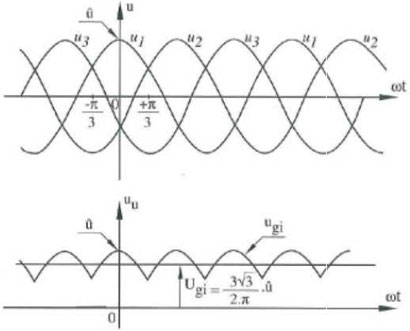
VFD controlled Induction motor ...
This paper presents a procedure to measure the efficiency on an induction motor fed by a VFD by the all operation range to speed ...
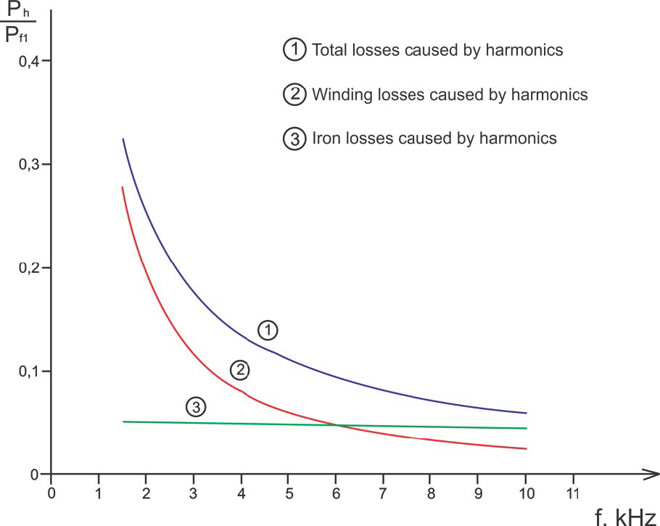
VFD: Pulse Width Modulation (PWM)
Pulse Width Modulation (PWM) VFDs provide a more sinusoidal current output to control frequency and voltage supplied to an AC ...
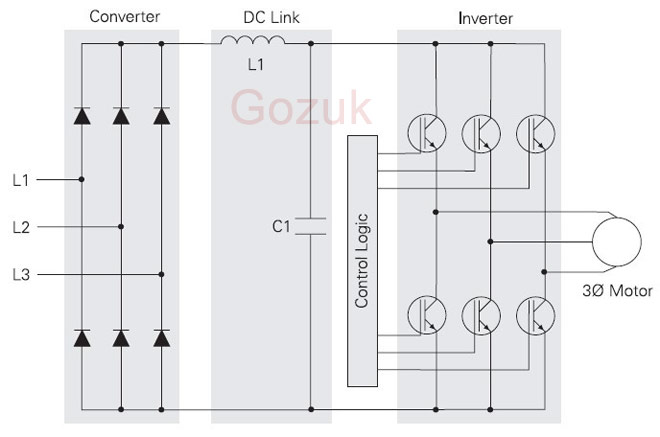
Variable frequency drive Advantages & ...
VFDs are good for variable speed, in a water pump this is used to maintain a steady pressure, they will smooth out variances in ...
Variable frequency drive Energy saving
Energy can be saved in a VFD by reducing the losses in the electric motor or by reducing the energy consumption of the variable ...
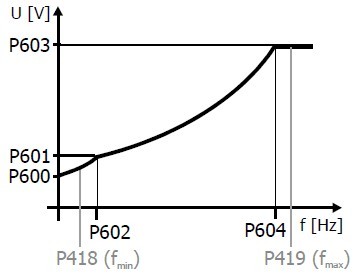
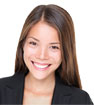
VFD manufacturers

