VFD control system in pump skid system
I designed and built a control system in the 90s for a "grease" pump skid system for a Goulds distributor who designed it for Texaco's lubricants division. The skid used VFD drive pumps for base products like the fatty-acids mixture. I worked with the skid packager to determine flow rate level controls and monitoring to make sure the NPSHr was not exceeded for the product for its vapor pressure since the stuff had to be heated to pump it.
I've also designed, built and maintained mechanical and electronic/computer control systems for LPG pipelines. Plucking a point on PSI, GPM and vapor pressure charts is one thing. Knowing where to pick it depending on application and location for monitoring, controls and safety shutdowns is another. There is no chart to show you how to design a control and monitoring system for this that I know of.
If someone is having difficulty with the concept, it might be more productive to talk about what happens when there isn't enough suction head. What eventually starts to happen is cavitation. The pump will continue to pump but slowly destroy itself before it stops pumping entirely. As the pressure drops, low pressure zones drop below the vapor pressure, and cavitation starts to happen. Eventually, as you lose even more head, the stuff just outright boils, and pumping stops for want of liquid.
Depending on what you're pumping, the boiling point of the liquid may become the governing variable. This all goes into deciding the required NPSH.
Then you have to look at the suction setup, and consider what it might look like in a year if it's likely to foul. Often, everything works fine when everything is clean, but as crud builds up, it gets into trouble. You have to know all of this to get a system that will be reliable. And often, it's not the pump that makes the difference, but the suction piping, and the placement of the pump. In extreme cases, it may be necessary to dig a pit for the pump to sit in.
So here we were standing in the middle of the floor talking to the plant engineer watching our pump send vibrations through the floor strong enough to rattle your teeth. How am i able to explain that the pump should not run at 2200 rpm when it is designed for 1400 rpm and that the reason for the noise is the lack of NPSHa, or cavitation. All I am told is that the pump was not pumping enough at 1400 rpm so they had to increase the speed with the variable frequency drive (VFD). All I could say was they could run the pump at the proper speed and put a second pump in the system, or replace the bearings regularly and get a replacement pump on order. I expect the pump to last less than three months.
Although i do have a good news story where one of my customers did listen to me. I walked into their pump station and told them the pump was activating. Not understanding what I was talking about, I started discussing the repairs they had done on the pump. They were replacing the bearings every three months, the impeller every 6 months and the casing every 12 months pumping clear water. I described the condition of the impeller and casing and told them I could fix the problem. I simply used the discharge valve to throttle the pump discharge. I showed them how to use sound to properly set the valve and left it to them. My competitor was not happy as they were no longer selling any parts to this customer. Their current pump will now last years.
They still have an NPSH requirement which must be met from within from the system design and/or selection process. VFDs are an anathema to the uneducated as in the minds of many noise equates to hard work. Little do they realize that slowing the pump down could gain them ca. 30% additional flow rate.
I've also designed, built and maintained mechanical and electronic/computer control systems for LPG pipelines. Plucking a point on PSI, GPM and vapor pressure charts is one thing. Knowing where to pick it depending on application and location for monitoring, controls and safety shutdowns is another. There is no chart to show you how to design a control and monitoring system for this that I know of.
If someone is having difficulty with the concept, it might be more productive to talk about what happens when there isn't enough suction head. What eventually starts to happen is cavitation. The pump will continue to pump but slowly destroy itself before it stops pumping entirely. As the pressure drops, low pressure zones drop below the vapor pressure, and cavitation starts to happen. Eventually, as you lose even more head, the stuff just outright boils, and pumping stops for want of liquid.
Depending on what you're pumping, the boiling point of the liquid may become the governing variable. This all goes into deciding the required NPSH.
Then you have to look at the suction setup, and consider what it might look like in a year if it's likely to foul. Often, everything works fine when everything is clean, but as crud builds up, it gets into trouble. You have to know all of this to get a system that will be reliable. And often, it's not the pump that makes the difference, but the suction piping, and the placement of the pump. In extreme cases, it may be necessary to dig a pit for the pump to sit in.
So here we were standing in the middle of the floor talking to the plant engineer watching our pump send vibrations through the floor strong enough to rattle your teeth. How am i able to explain that the pump should not run at 2200 rpm when it is designed for 1400 rpm and that the reason for the noise is the lack of NPSHa, or cavitation. All I am told is that the pump was not pumping enough at 1400 rpm so they had to increase the speed with the variable frequency drive (VFD). All I could say was they could run the pump at the proper speed and put a second pump in the system, or replace the bearings regularly and get a replacement pump on order. I expect the pump to last less than three months.
Although i do have a good news story where one of my customers did listen to me. I walked into their pump station and told them the pump was activating. Not understanding what I was talking about, I started discussing the repairs they had done on the pump. They were replacing the bearings every three months, the impeller every 6 months and the casing every 12 months pumping clear water. I described the condition of the impeller and casing and told them I could fix the problem. I simply used the discharge valve to throttle the pump discharge. I showed them how to use sound to properly set the valve and left it to them. My competitor was not happy as they were no longer selling any parts to this customer. Their current pump will now last years.
They still have an NPSH requirement which must be met from within from the system design and/or selection process. VFDs are an anathema to the uneducated as in the minds of many noise equates to hard work. Little do they realize that slowing the pump down could gain them ca. 30% additional flow rate.
Post a Comment:
You may also like:
Featured Articles
Non-Enclosure Variable Frequency Drive ...
No enclosure (cover), reducing installation space and cost effective. Widely used in All-In-One control cabinet. Keep the same ...
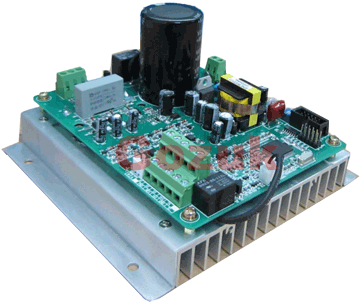
Variable frequency drive application ...
Variable Frequency Drive (VFD) can be used in lots of fields. Variable frequency drives are widely used to control the speed of ...
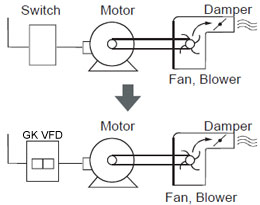
Variable frequency drive in HVAC ...
Variable frequency drives (VFD) have been used for HVAC systems in buildings for more than 40 years. But only in recent years, ...
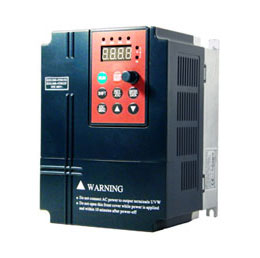
Variable Frequency Drive Harmonics and ...
A discussion of the benefits of variable frequency drives often leads to a question regarding electrical harmonic distortion ...
Three phase inverters
In the variable frequency drive rectifier paper, it explains how to go from three phase alternating current voltage to a direct ...
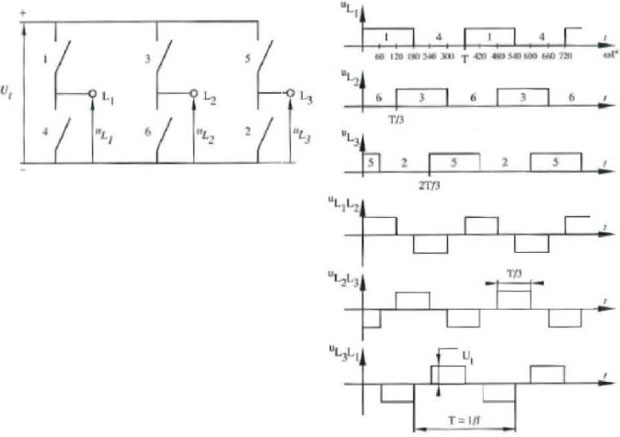
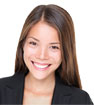
VFD manufacturers

