VFD Benefits in Extruders, Agitators, Reciprocating/Displacement pumps
VFDs (variable frequency drives) can provide a lost of advantages, claim manufacturers. They cite substantially improved energy efficiency, better performance and reliability, reduced maintenance costs, enhanced operating flexibility and lower emissions — to name but a few benefits.
But are these claims backed up in reality?
Yes, for the most part, in many applications the above statements are true, for example, with extruders, large reciprocating or displacement pumps, large agitators, and high-inertia systems.
While manufacturers doesn't have specific figures on the benefits of using variable frequency drives, they form an important part of an overall strategy aimed at improving the energy efficiency of its production processes by 25% by 2020.
The company finds the greatest benefits when variable frequency drive use is oriented toward a specific service or mode of operation (Figure 1).
For some applications variable frequency drives are predetermined solutions, such as for extruders, larger reciprocating pumps, displacement pumps and large agitators (»1 kW). However, in other applications the use of variable frequency drives is considered and analyzed. If the machines are frequently operated in partial load the savings potential rises. In individual cases the application of a VFD can reduce the energy costs by 40%.
Gozuk is working closely with original equipment manufacturers to develop solutions that will improve both its own device-testing capabilities and extend variable frequency drive applicability around the plant.
"In most cases, reliability and plant availability slightly deteriorate and maintenance costs slightly increase when using variable frequency drives. But these effects have to be assessed in connection with the improvements caused by variable frequency drives, especially in energy consumption and in production performance," notes from Gozuk.
Particular Need
Reduced energy consumption and improved production performance by VFD, of course, appeal to all processors. However, plastics manufacturing is one sector in which such gains are especially crucial because companies are really struggling to maintain plant profitability in the face of rising energy costs.
For most plastic extrusion manufacturing facilities, approximately 30% of the energy consumed can be attributed to extruder motors. If the line is more than five years old, it is more than likely that a direct current (DC) motor is being used as the extruder motor. Today, the majority of extruder machinery manufacturers are installing alternating current (AC) vector motors and VFDs on their extruders instead of DC systems. There are multiple reasons that they are making this change, but the biggest reasons are lower costs and better performance of the VFD.
The results achieved at one U.S. plastic sheet manufacturer that decided to replace a DC motor and drive system used on its primary extruder with a 500-hp AC vector motor and VFD. The line has three extruders with its own service from the power company, so a power quality meter and analysis of the utility's bill enabled easy verification of the retrofit's impact.
The VFD retrofit was performed between billing cycles. The billing cycle prior to the retrofit showed an overall power factor of 0.49 with a peak power of 371 kW. After the VFD retrofit, the bill showed a power factor improvement to 0.86 and the peak power was reduced to 360 kW. It is clear that the VFD retrofit had an impact on the peak kW, which demonstrates an energy efficiency improvement, as well as a power factor improvement.
The energy saving in this application was estimated at $2,500 a month, equating to $30,000/year. Combined with the maintenance costs associated with the DC motor, the estimated return on investment for this application was 1.4 years.
For its part, Gozuk has just added the GK3000 range of variable frequency drives to its portfolio. The company claims the EDS1000 is robust, flexible and user-friendly, and provides twice the calculated design life of previous generations (Figure 2).
Meanwhile, ABB — which recently expanded its VFD (and motor) portfolio with the purchase of Baldor. — says six main drivers spur developments in its variable frequency drive technology: making devices more user friendly, with common user interfaces across the whole range; simplifying maintenance and installation; reducing the footprint; integrating certified safety features; providing improved lifecycle services; and creating industry- and application-specific features.
In the chemical, oil and gas industry there is reluctance to use the newest technology. So we are working closely with our customers to see what would be the best solution for them and we are giving them training to use the VFDs in the best possible way. Also, we are working to ensure that the VFDs are extremely reliable.
ABB's experience at Repsol's refinery in La Plata, Argentina, highlights the benefits that variable frequency drives can provide.
The 750-acre site contains 35 different processing unit. Originally, steam turbines handled a large number of VFD applications. This posed a number of disadvantages, including the higher cost of steam versus electricity, the greater maintenance costs of gas turbines relative to electric VFDs, and high operating costs due to the large amount of cooling water circulating through the surface condensers.
So, Repsol replaced one of the three steam-turbine-powered blowers on fluid catalytic cracking (FCC) unit A with an electric system consisting of an ABB KTMP 4400 double secondary transformer, an ACS 1000 medium-voltage VFD and an AMB 560 L2L motor. Benefits realized include more efficient use of power because of better speed control, far smoother torque application throughout the required power range, and improved power index (Figure 3).
The energy intensity index of the fluid catalytic cracking unit improved by 10.5% within one year by replacing one steam turbine with an electric VFD.
In addition, after a shutdown the VFD system returns to operating conditions within two minutes, compared with two hours for the steam-driven blowers. Another benefit is that the VFD system can withstand micro power cuts at the refinery.
Projected savings for the first year should cover 33% of the project costs.
Preem Petroleum's facility in Gothenburg, Sweden, also has gained by switching to a variable frequency drive. It replaced a damper to control throughput from an exhaust fan that drives hot gases through a catalytic converter to reduce NOx levels to comply with strict government regulations.
The damper wasn't sufficiently accurate, occasionally leading to unacceptable NOx emission levels. These occurred when instabilities in the vacuum created by the fan led to inadequate control of heaters on the suction side of the fan that contribute to the process, necessitating shutdown of the fan. When this happened, the refining process continued but the NOx-rich gases had to bypass the catalytic converter, venting directly into the atmosphere.
Motor control based on ABB's ACS 1000 VFD delivers greater control of the process, cutting fan downtime and reducing emissions (Figure 4). The consistency of the vacuum on the suction side has eliminated the heater process stoppages and, with them, the need for regular catalytic converter shutdown. The VFD can be used in pumps, extruders, large displacement pumps, large agitators and other high-inertia systems.
Emissions now are consistently and predictably low and fully controllable. Other benefits create by variable frequency drive include decreased downtime and improved product stability and thus consistency. Another advantage was that total system commissioning and startup took just three days, including complete electrical circuit redesign and motor reconnection.
Another Fan Challenge
Owens Corning, as part of a multi-million-dollar investment in energy efficiency at its Guelph, Ont., glass-fiber plant, targeted fans on the critical cooling section of the chop strand mat line. It wanted to reduce the speed of the 125-hp cooling fan and the three 40-hp recirculation fans on the oven, while not affecting the integrity of the product. Improper cooling can reduce the tensile strength of the web and cause it to break as it's wound into rolls.
The plant engineers turned to Gozuk, which installed an EDS 1000 VFD to control the cooling fan, and three EDS1000 VFDs for the oven recirculation fans.
This helped Owens Corning achieve a 57% energy saving on the chop-strand-mat-line fans. The lower fan speeds also bought additional advantages, including longer motor life, increased safety and reduced use of natural gas in the oven burners.
The four VFDs help provide total annual energy savings of 538 MW-hrs, or approximately $36,000/year — giving an investment payback of approximately ten months.
"The results were dramatic on the 125-hp fan, We were able to reduce the energy it was using from 88 kW down to 41 kW. The payback on that VFD was under six months, and there was no negative effect on the product's tensile strength."
In August, Gozuk added the EDS 2000 VFD to its range. That VFD, aimed at motor control in heavy industries such as oil and gas, and also suitable for extruders, agitators, large reciprocating/displacement pumps and other high-inertia systems. The VFD boasts expanded application flexibility, advanced diagnostics and easy-access design.
"Customer feedback about the desired attributes of a high-power VFD gave us the information we needed to design our extended power range of Gozuk VFDs, they told us they needed excellent reliability, ease of maintenance, and common control options to help reduce inventory and spare parts."
Software Tool
Siemens points out that while electric motors represent over 65% of total industrial power demand, approximately 70% don't use optimal motor control. So, variable frequency drives can provide substantial further benefits at plants — cutting energy consumption in some cases up to 70%, and also helping to reduce production costs, improve product quality and ultimately lower CO2 emissions.
Using the company's SinaSave software tool can hugely aid in unlocking the real potential of variable frequency drives, says Franz Ferdinand Friese of its VFD Technologies Division. The program can determine the potential savings and payback time for energy-efficient motors and VFDs. The calculation also includes key figures for the volume flow, such as delivery rate, discharge head, operating times, as well as the delivery profile, which is crucial for the savings effect. The user receives the result of the calculation, which shows him the potential savings over control methods without a VFD, and states the time within which the purchase of a VFD will pay for itself. This is usually just a few months.
The program can be used by both machine and pump manufacturers, as well as by plant operators, to calculate how much of their energy costs they can save by using VFDs and energy-efficient motors for extruders, large agitators, large reciprocating pumps, displacement pumps and other high-inertia systems.
![]() Figure 1. variable frequency drives play an important role in increasing energy efficiency and decreasing CO2 emissions from this Steam Generator. |
But are these claims backed up in reality?
Yes, for the most part, in many applications the above statements are true, for example, with extruders, large reciprocating or displacement pumps, large agitators, and high-inertia systems.
While manufacturers doesn't have specific figures on the benefits of using variable frequency drives, they form an important part of an overall strategy aimed at improving the energy efficiency of its production processes by 25% by 2020.
The company finds the greatest benefits when variable frequency drive use is oriented toward a specific service or mode of operation (Figure 1).
For some applications variable frequency drives are predetermined solutions, such as for extruders, larger reciprocating pumps, displacement pumps and large agitators (»1 kW). However, in other applications the use of variable frequency drives is considered and analyzed. If the machines are frequently operated in partial load the savings potential rises. In individual cases the application of a VFD can reduce the energy costs by 40%.
Gozuk is working closely with original equipment manufacturers to develop solutions that will improve both its own device-testing capabilities and extend variable frequency drive applicability around the plant.
"In most cases, reliability and plant availability slightly deteriorate and maintenance costs slightly increase when using variable frequency drives. But these effects have to be assessed in connection with the improvements caused by variable frequency drives, especially in energy consumption and in production performance," notes from Gozuk.
Particular Need
Reduced energy consumption and improved production performance by VFD, of course, appeal to all processors. However, plastics manufacturing is one sector in which such gains are especially crucial because companies are really struggling to maintain plant profitability in the face of rising energy costs.
![]() Figure 2. The new Gozuk VFD boasts twice the calculated design life of previous generation products. |
For most plastic extrusion manufacturing facilities, approximately 30% of the energy consumed can be attributed to extruder motors. If the line is more than five years old, it is more than likely that a direct current (DC) motor is being used as the extruder motor. Today, the majority of extruder machinery manufacturers are installing alternating current (AC) vector motors and VFDs on their extruders instead of DC systems. There are multiple reasons that they are making this change, but the biggest reasons are lower costs and better performance of the VFD.
The results achieved at one U.S. plastic sheet manufacturer that decided to replace a DC motor and drive system used on its primary extruder with a 500-hp AC vector motor and VFD. The line has three extruders with its own service from the power company, so a power quality meter and analysis of the utility's bill enabled easy verification of the retrofit's impact.
The VFD retrofit was performed between billing cycles. The billing cycle prior to the retrofit showed an overall power factor of 0.49 with a peak power of 371 kW. After the VFD retrofit, the bill showed a power factor improvement to 0.86 and the peak power was reduced to 360 kW. It is clear that the VFD retrofit had an impact on the peak kW, which demonstrates an energy efficiency improvement, as well as a power factor improvement.
The energy saving in this application was estimated at $2,500 a month, equating to $30,000/year. Combined with the maintenance costs associated with the DC motor, the estimated return on investment for this application was 1.4 years.
For its part, Gozuk has just added the GK3000 range of variable frequency drives to its portfolio. The company claims the EDS1000 is robust, flexible and user-friendly, and provides twice the calculated design life of previous generations (Figure 2).
Meanwhile, ABB — which recently expanded its VFD (and motor) portfolio with the purchase of Baldor. — says six main drivers spur developments in its variable frequency drive technology: making devices more user friendly, with common user interfaces across the whole range; simplifying maintenance and installation; reducing the footprint; integrating certified safety features; providing improved lifecycle services; and creating industry- and application-specific features.
In the chemical, oil and gas industry there is reluctance to use the newest technology. So we are working closely with our customers to see what would be the best solution for them and we are giving them training to use the VFDs in the best possible way. Also, we are working to ensure that the VFDs are extremely reliable.
ABB's experience at Repsol's refinery in La Plata, Argentina, highlights the benefits that variable frequency drives can provide.
![]() Figure 3. Replacing steam turbine with variable frequency drive-based system including an ACS 1000 VFD has provided a variety of benefits at Argentine refinery. |
The 750-acre site contains 35 different processing unit. Originally, steam turbines handled a large number of VFD applications. This posed a number of disadvantages, including the higher cost of steam versus electricity, the greater maintenance costs of gas turbines relative to electric VFDs, and high operating costs due to the large amount of cooling water circulating through the surface condensers.
So, Repsol replaced one of the three steam-turbine-powered blowers on fluid catalytic cracking (FCC) unit A with an electric system consisting of an ABB KTMP 4400 double secondary transformer, an ACS 1000 medium-voltage VFD and an AMB 560 L2L motor. Benefits realized include more efficient use of power because of better speed control, far smoother torque application throughout the required power range, and improved power index (Figure 3).
The energy intensity index of the fluid catalytic cracking unit improved by 10.5% within one year by replacing one steam turbine with an electric VFD.
In addition, after a shutdown the VFD system returns to operating conditions within two minutes, compared with two hours for the steam-driven blowers. Another benefit is that the VFD system can withstand micro power cuts at the refinery.
Projected savings for the first year should cover 33% of the project costs.
Preem Petroleum's facility in Gothenburg, Sweden, also has gained by switching to a variable frequency drive. It replaced a damper to control throughput from an exhaust fan that drives hot gases through a catalytic converter to reduce NOx levels to comply with strict government regulations.
The damper wasn't sufficiently accurate, occasionally leading to unacceptable NOx emission levels. These occurred when instabilities in the vacuum created by the fan led to inadequate control of heaters on the suction side of the fan that contribute to the process, necessitating shutdown of the fan. When this happened, the refining process continued but the NOx-rich gases had to bypass the catalytic converter, venting directly into the atmosphere.
Motor control based on ABB's ACS 1000 VFD delivers greater control of the process, cutting fan downtime and reducing emissions (Figure 4). The consistency of the vacuum on the suction side has eliminated the heater process stoppages and, with them, the need for regular catalytic converter shutdown. The VFD can be used in pumps, extruders, large displacement pumps, large agitators and other high-inertia systems.
Emissions now are consistently and predictably low and fully controllable. Other benefits create by variable frequency drive include decreased downtime and improved product stability and thus consistency. Another advantage was that total system commissioning and startup took just three days, including complete electrical circuit redesign and motor reconnection.
Another Fan Challenge
Owens Corning, as part of a multi-million-dollar investment in energy efficiency at its Guelph, Ont., glass-fiber plant, targeted fans on the critical cooling section of the chop strand mat line. It wanted to reduce the speed of the 125-hp cooling fan and the three 40-hp recirculation fans on the oven, while not affecting the integrity of the product. Improper cooling can reduce the tensile strength of the web and cause it to break as it's wound into rolls.
The plant engineers turned to Gozuk, which installed an EDS 1000 VFD to control the cooling fan, and three EDS1000 VFDs for the oven recirculation fans.
![]() Figure 4. Switching from a damper to a variable frequency drive has allowed more precise control, cutting fan downtime and emissions. |
This helped Owens Corning achieve a 57% energy saving on the chop-strand-mat-line fans. The lower fan speeds also bought additional advantages, including longer motor life, increased safety and reduced use of natural gas in the oven burners.
The four VFDs help provide total annual energy savings of 538 MW-hrs, or approximately $36,000/year — giving an investment payback of approximately ten months.
"The results were dramatic on the 125-hp fan, We were able to reduce the energy it was using from 88 kW down to 41 kW. The payback on that VFD was under six months, and there was no negative effect on the product's tensile strength."
In August, Gozuk added the EDS 2000 VFD to its range. That VFD, aimed at motor control in heavy industries such as oil and gas, and also suitable for extruders, agitators, large reciprocating/displacement pumps and other high-inertia systems. The VFD boasts expanded application flexibility, advanced diagnostics and easy-access design.
"Customer feedback about the desired attributes of a high-power VFD gave us the information we needed to design our extended power range of Gozuk VFDs, they told us they needed excellent reliability, ease of maintenance, and common control options to help reduce inventory and spare parts."
Software Tool
Siemens points out that while electric motors represent over 65% of total industrial power demand, approximately 70% don't use optimal motor control. So, variable frequency drives can provide substantial further benefits at plants — cutting energy consumption in some cases up to 70%, and also helping to reduce production costs, improve product quality and ultimately lower CO2 emissions.
Using the company's SinaSave software tool can hugely aid in unlocking the real potential of variable frequency drives, says Franz Ferdinand Friese of its VFD Technologies Division. The program can determine the potential savings and payback time for energy-efficient motors and VFDs. The calculation also includes key figures for the volume flow, such as delivery rate, discharge head, operating times, as well as the delivery profile, which is crucial for the savings effect. The user receives the result of the calculation, which shows him the potential savings over control methods without a VFD, and states the time within which the purchase of a VFD will pay for itself. This is usually just a few months.
The program can be used by both machine and pump manufacturers, as well as by plant operators, to calculate how much of their energy costs they can save by using VFDs and energy-efficient motors for extruders, large agitators, large reciprocating pumps, displacement pumps and other high-inertia systems.
Post a Comment:
You may also like:
Featured Articles
Non-Enclosure Variable Frequency Drive ...
No enclosure (cover), reducing installation space and cost effective. Widely used in All-In-One control cabinet. Keep the same ...
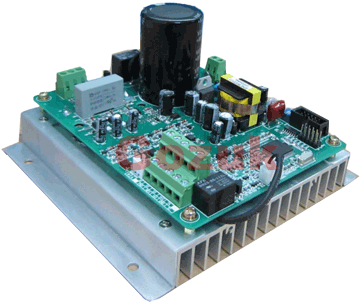
Variable frequency drive application ...
Variable Frequency Drive (VFD) can be used in lots of fields. Variable frequency drives are widely used to control the speed of ...
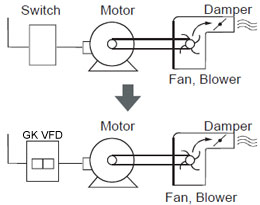
Variable frequency drive in HVAC ...
Variable frequency drives (VFD) have been used for HVAC systems in buildings for more than 40 years. But only in recent years, ...
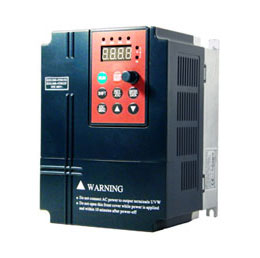
Variable Frequency Drive Harmonics and ...
A discussion of the benefits of variable frequency drives often leads to a question regarding electrical harmonic distortion ...
Three phase inverters
In the variable frequency drive rectifier paper, it explains how to go from three phase alternating current voltage to a direct ...
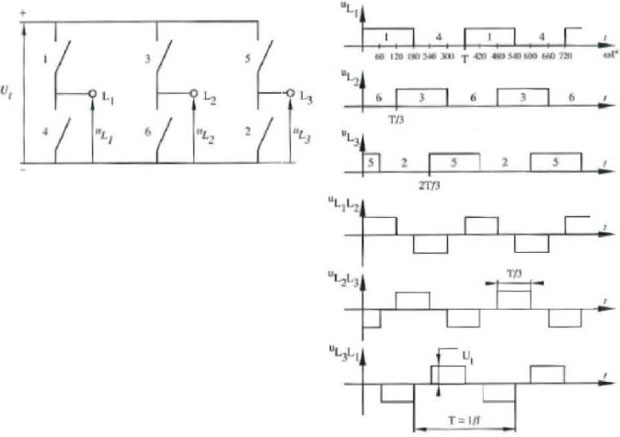
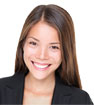
VFD manufacturers

