V/F drive or Vector drive for a furnace door?
Q: I am currently using a V/F drive to control the forward/backward movement of a bogie and upward/downward movement of the door on a furnace. I am unable to achieve instantaneous stop of the doors. Can you suggest a remedy for this? Will using a braking resistor on the present variable frequency drive improve the situation? Do I need to use a vector VFD for this application?
A: There are too many unknowns. What size of the variable frequency drive? What is the inertia of the load? What is the speed? What is the acceleration/ deceleration time? Is it direct driven or through a gear box? If you need to control torque a vector variable frequency drive that gives access to the current or torque loop would be required. Do you have any feedback control? Do you have access to the DC bus so a brake chopper could be connected? If you use a brake chopper, the load inertia, time and stored energy are critical for sizing the resistor. This also assures the DC bus does not overvoltage and the brake IGBT current rating is not exceeded.
The inertia of the mechanical system and the required door speed will ultimately direct the best solution. However, "instantaneous" stop is physically impossible. You must decelerate, no matter how short the deceleration window is. With a VFD, I will usually opt for analog motion control or speed vector control with an anticipatory deceleration sensor. Depending on the system inertia, you may also need to add a DB resistor.
Another possibility is to use a VFD with DC braking capability. DC braking applies DC across one set of legs of the motor and stops it quicker, but at the cost of additional heating in the motor. One needs to consider the cycle times of the system and possibly up size the motor to handle this.
A: There are too many unknowns. What size of the variable frequency drive? What is the inertia of the load? What is the speed? What is the acceleration/ deceleration time? Is it direct driven or through a gear box? If you need to control torque a vector variable frequency drive that gives access to the current or torque loop would be required. Do you have any feedback control? Do you have access to the DC bus so a brake chopper could be connected? If you use a brake chopper, the load inertia, time and stored energy are critical for sizing the resistor. This also assures the DC bus does not overvoltage and the brake IGBT current rating is not exceeded.
The inertia of the mechanical system and the required door speed will ultimately direct the best solution. However, "instantaneous" stop is physically impossible. You must decelerate, no matter how short the deceleration window is. With a VFD, I will usually opt for analog motion control or speed vector control with an anticipatory deceleration sensor. Depending on the system inertia, you may also need to add a DB resistor.
Another possibility is to use a VFD with DC braking capability. DC braking applies DC across one set of legs of the motor and stops it quicker, but at the cost of additional heating in the motor. One needs to consider the cycle times of the system and possibly up size the motor to handle this.
Injection braking will be ok provided the system can handle it. There is stored energy in the moving door system. In the case he wants to stop the door instantaneously. Is the motor connected directly or through a gear box? What type couplings are used? On what physical parameters were the motor and drive sized? Was acceleration torque taken into account? What is the service factor for the motor? What is the current rating of the drive in relation to the motor? How are the doors mounted?
Like close loop control, braking resistors, DC injection barking are the solutions to have better response on the desired activity. However based on the application and other aspects like inertia, speed on which to be stopped, GB ratio, etc., the correct combinations to be arrived.
With braking resistor, install "slow down" travel path limit switch just before the full closing of door. On getting the signal from the slow down limit switch, issue stop command to the variable frequency drive.
We use such approach in container handling cranes. It works 100%
You may have to position the slow down limit switch properly during commissioning to have perfect and smooth closing.
We use such approach in container handling cranes. It works 100%
You may have to position the slow down limit switch properly during commissioning to have perfect and smooth closing.
Post a Comment:
You may also like:
Featured Articles
Non-Enclosure Variable Frequency Drive ...
No enclosure (cover), reducing installation space and cost effective. Widely used in All-In-One control cabinet. Keep the same ...
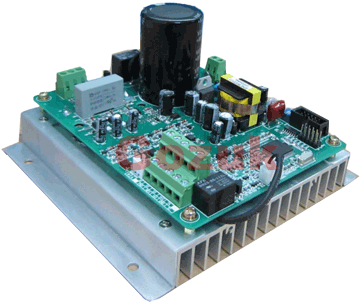
Variable frequency drive application ...
Variable Frequency Drive (VFD) can be used in lots of fields. Variable frequency drives are widely used to control the speed of ...
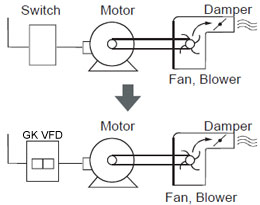
Variable frequency drive in HVAC ...
Variable frequency drives (VFD) have been used for HVAC systems in buildings for more than 40 years. But only in recent years, ...
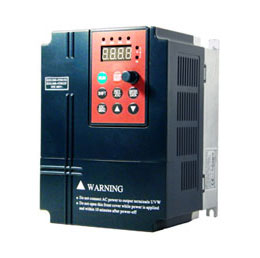
Variable Frequency Drive Harmonics and ...
A discussion of the benefits of variable frequency drives often leads to a question regarding electrical harmonic distortion ...
Three phase inverters
In the variable frequency drive rectifier paper, it explains how to go from three phase alternating current voltage to a direct ...
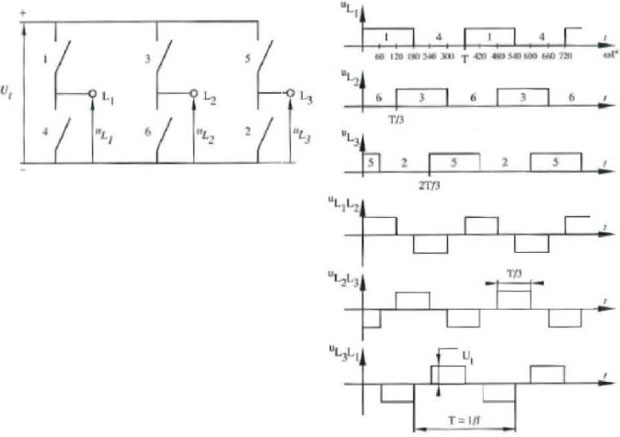
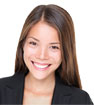
VFD manufacturers

