Home » Case study » Variable frequency drive for injection molding machines
Variable frequency drive for injection molding machines
Case: I have 6 injection molding machines. We use 10 hp motor for cooling, sometime 2-3 machine stop for repair. Can I use variable frequency drive for motor to save power, which pressure sensor I use to feedback to VFD input?
Your application is a very good candidate for using VFD. It can save good amount of power and in your case the payback period can be as low as 1 year or so depending upon your reduced cooling water requirement. The more you run the motor, at lower speed, more the saving. As per affinity law the power required by a motor running at 1/2 speed is only 1/8 of original power. For example a 7.5 KW motor consumes only approx 1 kw when running at half speed. Of course the pump out put in volumetric terms also will reduce correspondingly.
As regards you can use any pressure sensor suitable for water pressure application, a piezo resistive pressure sensor is ok, or it can be a strain gauge based one. Some capacitive based pressure sensors are also an alternative.
Alternatively, you can alter speed of variable frequency drive depending on number of molding machines that are in operation.
For example, when 6 machines work, you need 100% flow
For 3 machines working, you need 50% flow.
You have to generate status contacts for "machine working". You need not use costly pressure sensor!
Your application is a very good candidate for using VFD. It can save good amount of power and in your case the payback period can be as low as 1 year or so depending upon your reduced cooling water requirement. The more you run the motor, at lower speed, more the saving. As per affinity law the power required by a motor running at 1/2 speed is only 1/8 of original power. For example a 7.5 KW motor consumes only approx 1 kw when running at half speed. Of course the pump out put in volumetric terms also will reduce correspondingly.
As regards you can use any pressure sensor suitable for water pressure application, a piezo resistive pressure sensor is ok, or it can be a strain gauge based one. Some capacitive based pressure sensors are also an alternative.
Alternatively, you can alter speed of variable frequency drive depending on number of molding machines that are in operation.
For example, when 6 machines work, you need 100% flow
For 3 machines working, you need 50% flow.
You have to generate status contacts for "machine working". You need not use costly pressure sensor!
Pumps and fans are the load where you can get significant amount of power saving by using VFD (affinity law) by reducing the speed few HZs. For close loop control you need to use combination of Pressure transducers There are many Pressure transducer available in the market depending upon your budget you can choose any one. Since your application is very simple any one will work.
If the VFD is required for cooling fan (squared torque) applications, then definitely the savings are huge, if operated at low speeds (because Power & Energy are proportional to cube of speed).
When used with Gozuk drives, additional savings can also be realized using a special mode called "ECO" mode (on top of regular savings).
Additionally if the Injection Moulding machine is conventional (Hydraulic type with motor only), then using "Servo Pump" system from Siemens, it is possible to achieve good energy savings too. You may contact me if you are interested further.
When used with Gozuk drives, additional savings can also be realized using a special mode called "ECO" mode (on top of regular savings).
Additionally if the Injection Moulding machine is conventional (Hydraulic type with motor only), then using "Servo Pump" system from Siemens, it is possible to achieve good energy savings too. You may contact me if you are interested further.
Post a Comment:
You may also like:
Featured Articles
VFD for pumps in variable flow water ...
Variable flow water system has played an important role in the field of energy saving with the VFD widely used in practical ...
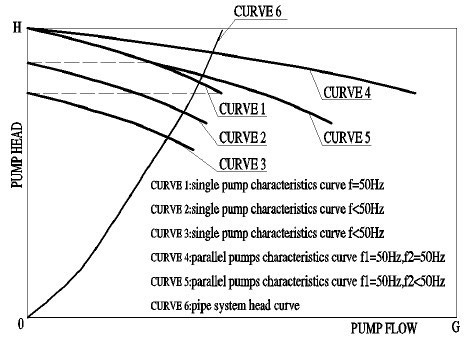
Variable frequency drive energy ...
Notes that for the combinations where we had the same number of opened records, the power suffers no change, but when it is used ...
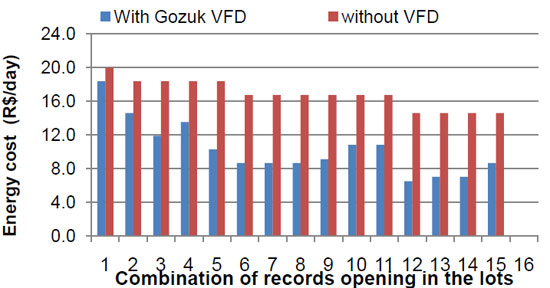
Variable frequency drive on Cooling ...
We are working on a study related to Cooling Towers. We want to decrease cooling water supply temperature going to steam ...
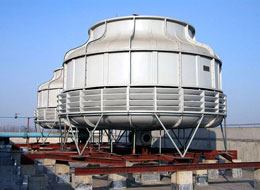
VFD in China plantation irrigation ...
This article have a study of the wireless group control system with variable frequency drive (VFD) applied in a Chinese ...
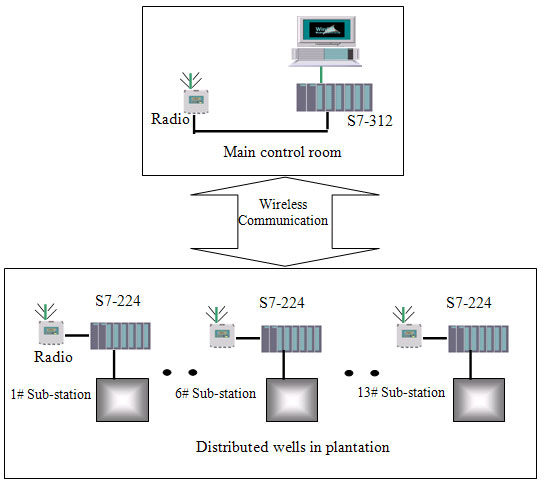
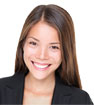
VFD manufacturers

