Replace DC system with AC system
When I attempt to replace a DC system with an AC system, there are a few fundamental questions that I must answer.
1) What is the worst-case torque requirement, and at what speed?
2) What is the full range of speed? (Including, does it need to reverse?)
3) Does the motor need to provide braking or holding torque?
4) How precise does the speed control need to be?
Generally, an AC motor can produce 100% of the motor rated torque at any speed, if applied on a good quality variable frequency drive (VFD). If 100% torque is required for long periods at zero or very low speed (below, say 5Hz or 1/10 of base speed) then a speed feedback device (tach, encoder, resolver) will probably be needed. Also, auxiliary cooling or other measures will be necessary to prevent motor thermal failure.
Once the worst-case torque and speed requirements are determined, the required motor power can be calculated. For example, if your application requires 20 ft.-lbs. of torque at 635 RPM continuously, and has an operating speed range of -1750RPM to +1750RPM, but the torque at 1750RPM is much less than the torque at 635RPM (this example is a drive table for a machine tool - the table pushes a fixture through a machining operation at 635RPM, but once the cut is complete, it retracts at maximum speed with almost no load) then you need an AC motor capable of producing 20 ft.-lbs of torque at its base speed, but is capable of spinning 1750RPM.
The full-load rated torque of a 7.5Hp 4-pole motor with a base speed of 1775 RPM is 22.5 ft.-lbs. Any good quality VFD will allow you to generate this torque at any speed between about 20RPM and 1750RPM. You could also select a 5Hp 1175RPM motor and drive, and overspeed the motor to 90Hz to reach 1750RPM on extraction - the lack of available torque at high speed is not a hindrance in this application.
You must understand the torque requirements of the application to properly apply a drive system, AC or DC. Then add to that you must understand the speed requirements to determine whether closed-loop control is necessary, and whether regenerative power (dynamic braking) is necessary. Thirdly, you must understand the environmental conditions under which the system operates so that you can properly compensate for protection of the motor and the drive (thermal, dust, liquid, explosive atmosphere, etc.) Finally, you must understand any other special conditions of the application - for example, the variable frequency drive for the motor cannot be placed any closer than 400 meters away, or only single-phase power is available at the site, etc. It's not simply a matter of converting kW to HP.
1) What is the worst-case torque requirement, and at what speed?
2) What is the full range of speed? (Including, does it need to reverse?)
3) Does the motor need to provide braking or holding torque?
4) How precise does the speed control need to be?
Generally, an AC motor can produce 100% of the motor rated torque at any speed, if applied on a good quality variable frequency drive (VFD). If 100% torque is required for long periods at zero or very low speed (below, say 5Hz or 1/10 of base speed) then a speed feedback device (tach, encoder, resolver) will probably be needed. Also, auxiliary cooling or other measures will be necessary to prevent motor thermal failure.
Once the worst-case torque and speed requirements are determined, the required motor power can be calculated. For example, if your application requires 20 ft.-lbs. of torque at 635 RPM continuously, and has an operating speed range of -1750RPM to +1750RPM, but the torque at 1750RPM is much less than the torque at 635RPM (this example is a drive table for a machine tool - the table pushes a fixture through a machining operation at 635RPM, but once the cut is complete, it retracts at maximum speed with almost no load) then you need an AC motor capable of producing 20 ft.-lbs of torque at its base speed, but is capable of spinning 1750RPM.
The full-load rated torque of a 7.5Hp 4-pole motor with a base speed of 1775 RPM is 22.5 ft.-lbs. Any good quality VFD will allow you to generate this torque at any speed between about 20RPM and 1750RPM. You could also select a 5Hp 1175RPM motor and drive, and overspeed the motor to 90Hz to reach 1750RPM on extraction - the lack of available torque at high speed is not a hindrance in this application.
You must understand the torque requirements of the application to properly apply a drive system, AC or DC. Then add to that you must understand the speed requirements to determine whether closed-loop control is necessary, and whether regenerative power (dynamic braking) is necessary. Thirdly, you must understand the environmental conditions under which the system operates so that you can properly compensate for protection of the motor and the drive (thermal, dust, liquid, explosive atmosphere, etc.) Finally, you must understand any other special conditions of the application - for example, the variable frequency drive for the motor cannot be placed any closer than 400 meters away, or only single-phase power is available at the site, etc. It's not simply a matter of converting kW to HP.
In most practical application torque design data is not available, specially when a case of replacement is coming in a running plant. For AC variable frequency Drive, consider 150% long time overtorque capacity, while for DC consider 250% over torque. Thus a safe (but may be oversized) way is 2.5/1.5 times size for AC compared to DC. Thus in practice, will come down to Two frame size higher. e.g. replacement of 30kW DC by 45kW AC (both being 1500 rpm)
Post a Comment:
You may also like:
Featured Articles
What is VFD, How it works? - VFD ...
VFD is shorted for Variable Frequency Drive (also known as AC Drives and Inverters) -- that's used to make an AC motor working in ...
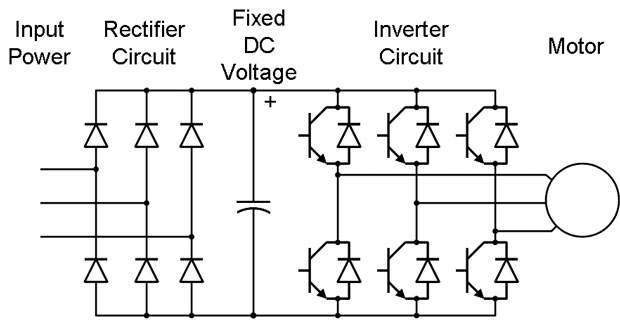
Variable frequency drive Rectifier
To understand variable frequency drive (VFD) better, it's necessary to explain some of the main parts of the variable frequency ...
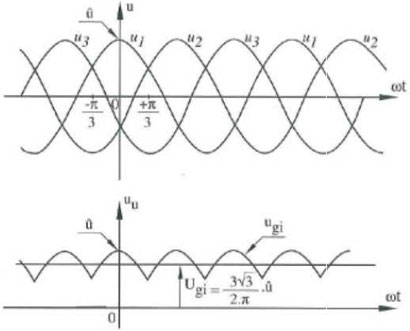
VFD: Insulated Gate Bipolar Transistor ...
IGBT (insulated gate bipolar transistor) provides a high switching speed necessary for PWM VFD operation. IGBTs are capable of ...
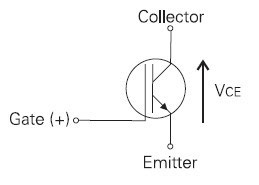
Three phase inverters
In the variable frequency drive rectifier paper, it explains how to go from three phase alternating current voltage to a direct ...
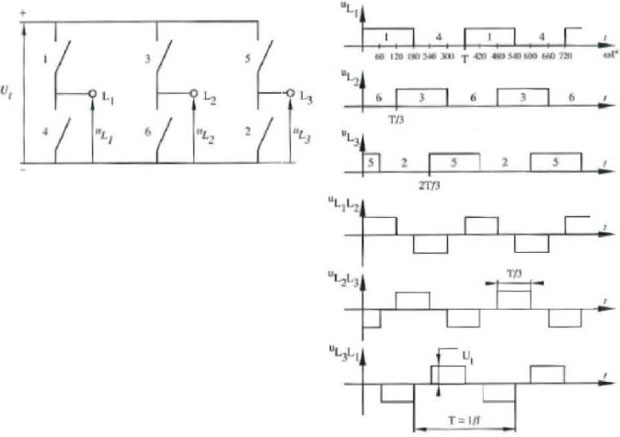
Variable Frequency Drive Harmonics and ...
A discussion of the benefits of variable frequency drives often leads to a question regarding electrical harmonic distortion ...
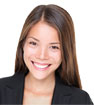
VFD manufacturers

