Main factors for better life cycle of centrifugal pumps
The first is that the system head has been calculated correctly. Very often the fear of falling short results in the pump head being overstated. In a good case the result will be a flow exceeding design. In a worst case cavitation can occur dramatically reducing both pump and seal life.
So, assuming the pump is properly sized, the life cycle is more often related to starts and stops. The more frequent the start/stop the shorter the pump life. The adverse effect of repeated starting can be lessened by using a soft starter or variable frequency drive to bring the pump on line slower that the direct on-line start. A variable frequency drive can also allow for fine tuning the system and adapting to changing system conditions such as a widely variable suction head or changes in viscosity.
You want to be sure the pump is sized correctly and applied properly for the application. Better life cycle can be achieved by proper operation (within the recommended operating range as described by the pump manufacturer) and through proper maintenance.
One of the more common problems associated with pump life cycle not meeting expectations is net positive suction head availability. Suction problems lead to cavitation and vibration.
Operate the pump as close to BEP as possible, preferably in the range of 80 to 110% of BEP with adequate NPSHa. Hydraulic forces on the pump are minimized by doing this significantly reducing pump stress.
It is very important to explain to the pump manufacturer what you are planning to do, secondly operate your pump as close to the design parameters as is realistically possible. This is not a given point, but more like a window in which the pump should operate. Within the different types of industry we are trying to make money, so it is very tempting to increase outputs of pumps to increase production, this is not uncommon. Even when changing outputs of pumps it is still possible to run the pump near its curve and prevent damages by all kinds of causes, this kind of operation requires some in depth knowledge of pump-operation.
So, assuming the pump is properly sized, the life cycle is more often related to starts and stops. The more frequent the start/stop the shorter the pump life. The adverse effect of repeated starting can be lessened by using a soft starter or variable frequency drive to bring the pump on line slower that the direct on-line start. A variable frequency drive can also allow for fine tuning the system and adapting to changing system conditions such as a widely variable suction head or changes in viscosity.
You want to be sure the pump is sized correctly and applied properly for the application. Better life cycle can be achieved by proper operation (within the recommended operating range as described by the pump manufacturer) and through proper maintenance.
One of the more common problems associated with pump life cycle not meeting expectations is net positive suction head availability. Suction problems lead to cavitation and vibration.
Operate the pump as close to BEP as possible, preferably in the range of 80 to 110% of BEP with adequate NPSHa. Hydraulic forces on the pump are minimized by doing this significantly reducing pump stress.
It is very important to explain to the pump manufacturer what you are planning to do, secondly operate your pump as close to the design parameters as is realistically possible. This is not a given point, but more like a window in which the pump should operate. Within the different types of industry we are trying to make money, so it is very tempting to increase outputs of pumps to increase production, this is not uncommon. Even when changing outputs of pumps it is still possible to run the pump near its curve and prevent damages by all kinds of causes, this kind of operation requires some in depth knowledge of pump-operation.
Post a Comment:
You may also like:
Featured Articles
Variable frequency drive Rectifier
To understand variable frequency drive (VFD) better, it's necessary to explain some of the main parts of the variable frequency ...
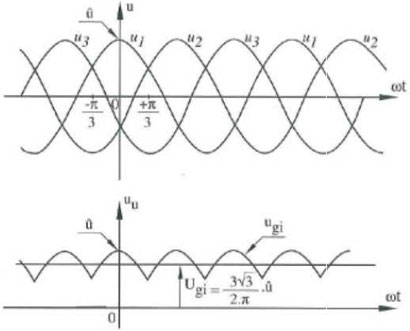
What is VFD, How it works? - VFD ...
VFD is shorted for Variable Frequency Drive (also known as AC Drives and Inverters) -- that's used to make an AC motor working in ...
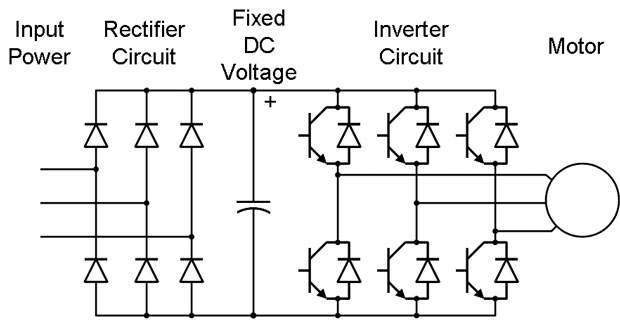
VFD: Insulated Gate Bipolar Transistor ...
IGBT (insulated gate bipolar transistor) provides a high switching speed necessary for PWM VFD operation. IGBTs are capable of ...
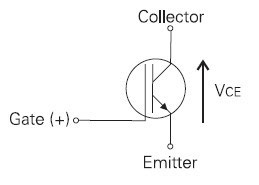
Three phase inverters
In the variable frequency drive rectifier paper, it explains how to go from three phase alternating current voltage to a direct ...
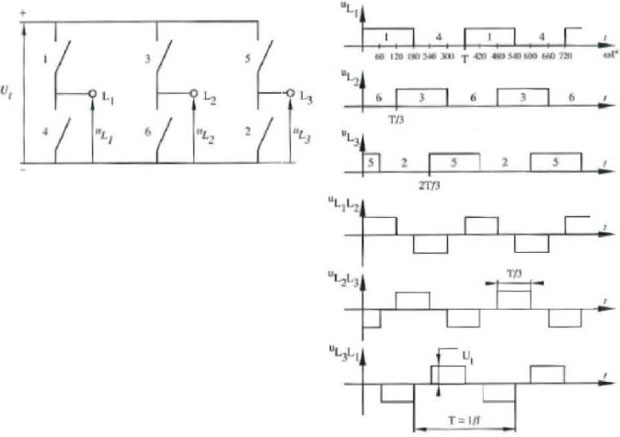
VFD controlled Induction motor ...
This paper presents a procedure to measure the efficiency on an induction motor fed by a VFD by the all operation range to speed ...
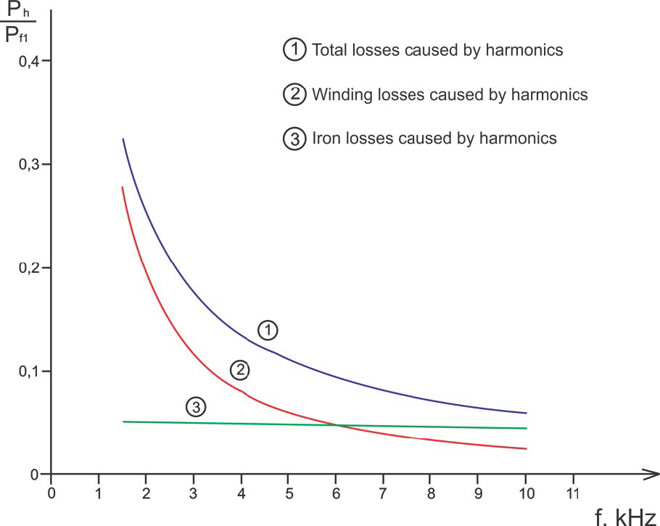
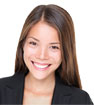
VFD manufacturers

