Estimate motor life expectancy
By now we learned that in reality it is extremely difficult to estimate motor life expectancy due to numerous different failure mechanisms that can show up along it operational life expectancy and surprise you, while you cannot predict everything. Therefore I still think that experience and cooperation with part suppliers (bearings, magnets, electronics...) is very important.
We were actually asking ourselves the same question about 5 years ago when our company started production of larger fan motors for air conditioning systems which can run non-stop for about 10 years.
Considering only bearings for instance you can experience end of life with flacking, grease contamination, electrical pitting, grease evaporation, grease oxidation, controlled by VFD, etc... most of those mechanisms can be estimated (see IEEE literature). Fatigue life time (flacking) for instance can be estimate with ISO 281 (2007) or even with online tools. But I can tell you that all those tools methods will never be able to include all the influential parameters. For instance our main bearing suppliers claim that those methods are just a toy for those who have no idea or for those who have no past experience.
Mathematics and models come after the improvement was done; therefore, I worry is about improving process and its components. I validate critical parameters and after I design component based on what it is required for the application.
If you would like to set an accelerated test first of all you should first consider main failure mechanisms and most influential parameters (voltage, rpm, humidity, temperature...). Then the best option would be to do the test at accelerated conditions.
We were actually asking ourselves the same question about 5 years ago when our company started production of larger fan motors for air conditioning systems which can run non-stop for about 10 years.
Considering only bearings for instance you can experience end of life with flacking, grease contamination, electrical pitting, grease evaporation, grease oxidation, controlled by VFD, etc... most of those mechanisms can be estimated (see IEEE literature). Fatigue life time (flacking) for instance can be estimate with ISO 281 (2007) or even with online tools. But I can tell you that all those tools methods will never be able to include all the influential parameters. For instance our main bearing suppliers claim that those methods are just a toy for those who have no idea or for those who have no past experience.
Mathematics and models come after the improvement was done; therefore, I worry is about improving process and its components. I validate critical parameters and after I design component based on what it is required for the application.
If you would like to set an accelerated test first of all you should first consider main failure mechanisms and most influential parameters (voltage, rpm, humidity, temperature...). Then the best option would be to do the test at accelerated conditions.
Post a Comment:
You may also like:
Featured Articles
Non-Enclosure Variable Frequency Drive ...
No enclosure (cover), reducing installation space and cost effective. Widely used in All-In-One control cabinet. Keep the same ...
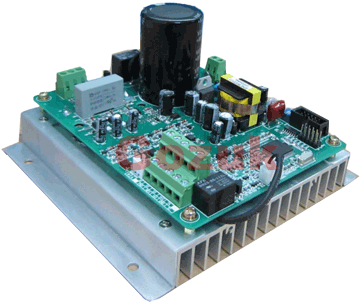
Variable frequency drive application ...
Variable Frequency Drive (VFD) can be used in lots of fields. Variable frequency drives are widely used to control the speed of ...
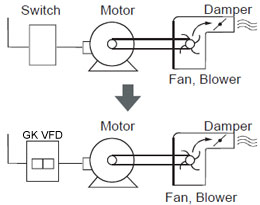
Variable frequency drive in HVAC ...
Variable frequency drives (VFD) have been used for HVAC systems in buildings for more than 40 years. But only in recent years, ...
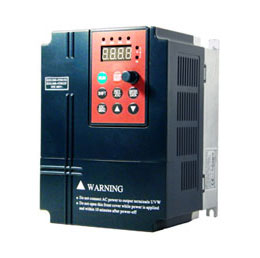
Variable Frequency Drive Harmonics and ...
A discussion of the benefits of variable frequency drives often leads to a question regarding electrical harmonic distortion ...
Three phase inverters
In the variable frequency drive rectifier paper, it explains how to go from three phase alternating current voltage to a direct ...
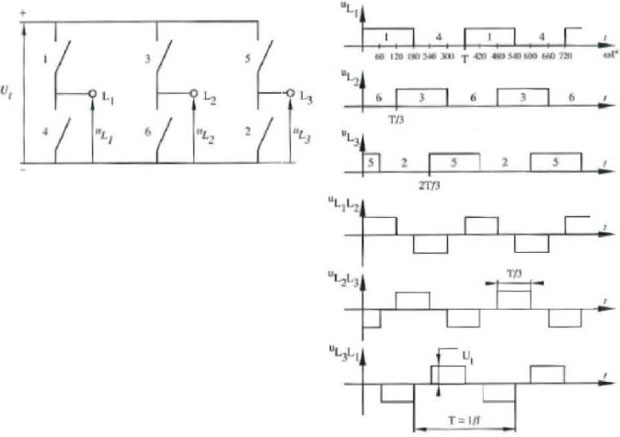
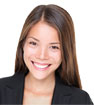
VFD manufacturers

