Home » Troubleshooting » Dual VFDs philosophy (on the same shaft) for critical fan/blower
Dual VFDs philosophy (on the same shaft) for critical fan/blower
Case: If we are having a dual drive philosophy for a fan/blower - arrangement is such that VFD driven motor is in operation and there is a standby motor (Direct on line starter) on the same shaft with declutch arrangement. Will it be possible for the standby motor to take full load in case VFD driven motor trip with in say 7-10 seconds? If yes what is the best possible arrangement/solution for such critical application if we want to avoid the trip. If anyone having idea about over-running or freewheeling movement (with clutch armament) - which one is recommended and what are the pros and cons of each philosophy.
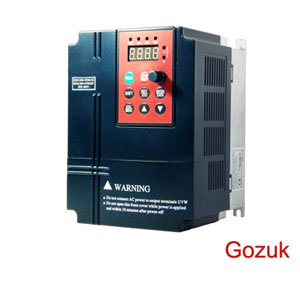
Look at the suitability of the drive train as a whole. Is the train motor-motor-load, or motor-load-motor? In the first case, whichever motor is closer to the load will have its shaft always spinning. In the event of a fault, this could result in further damage to the unit.
Look at reclose capability (particularly for line-start version). Check line-start machine's torque/speed profile against the proposed running speeds for the VFD version. For example: at 7 seconds into the acceleration, how much torque is required? If the line-start machine does not have AT LEAST that much locked rotor torque, you'll likely lose the load (and/or damage the line-start machine as well).
Figure out how fast the clutch system works: is it going to be fast enough to catch the load before it slows too much / the supply and terminal voltage varies too widely? Typical limits to initiate a "fast reclose" or "fast bus transfer" are on the order of 5-7 cycles (0.08 - 0.12 seconds).
A question that should be addressed is what failure mechanism you are designing to. Do you consider the only failure to be covered is failure of the VFD or do you want to consider failure of the blower or motor? If your risk analysis can discount failure of the blower or/and motor either for mechanical or electrical than a single blower + single motor installation could be acceptable. Such a system would be much simpler than having two motors on a single shaft and some sort of clutching arrangement. With a single blower/motor installation you could then have two VFD that could supply the motor. There are a variety of arrangements for connecting multiple drives to a single motor, i.e., master/slave, both energized, etc. With two motors on one shaft and they are both spinning with one energized, when you connect the energized motor to the line there will be a significant inrush current that the power system must be capable of handling.
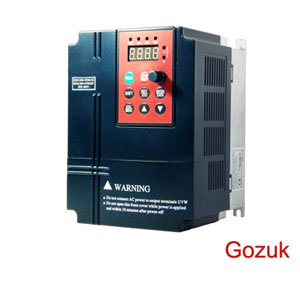
Look at the suitability of the drive train as a whole. Is the train motor-motor-load, or motor-load-motor? In the first case, whichever motor is closer to the load will have its shaft always spinning. In the event of a fault, this could result in further damage to the unit.
Look at reclose capability (particularly for line-start version). Check line-start machine's torque/speed profile against the proposed running speeds for the VFD version. For example: at 7 seconds into the acceleration, how much torque is required? If the line-start machine does not have AT LEAST that much locked rotor torque, you'll likely lose the load (and/or damage the line-start machine as well).
Figure out how fast the clutch system works: is it going to be fast enough to catch the load before it slows too much / the supply and terminal voltage varies too widely? Typical limits to initiate a "fast reclose" or "fast bus transfer" are on the order of 5-7 cycles (0.08 - 0.12 seconds).
A question that should be addressed is what failure mechanism you are designing to. Do you consider the only failure to be covered is failure of the VFD or do you want to consider failure of the blower or motor? If your risk analysis can discount failure of the blower or/and motor either for mechanical or electrical than a single blower + single motor installation could be acceptable. Such a system would be much simpler than having two motors on a single shaft and some sort of clutching arrangement. With a single blower/motor installation you could then have two VFD that could supply the motor. There are a variety of arrangements for connecting multiple drives to a single motor, i.e., master/slave, both energized, etc. With two motors on one shaft and they are both spinning with one energized, when you connect the energized motor to the line there will be a significant inrush current that the power system must be capable of handling.
Post a Comment:
You may also like:
Featured Articles
Non-Enclosure Variable Frequency Drive ...
No enclosure (cover), reducing installation space and cost effective. Widely used in All-In-One control cabinet. Keep the same ...
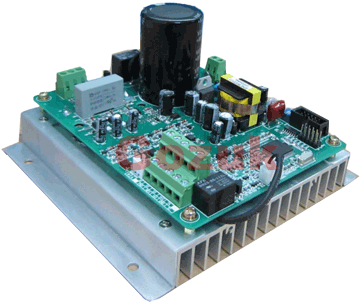
Variable frequency drive application ...
Variable Frequency Drive (VFD) can be used in lots of fields. Variable frequency drives are widely used to control the speed of ...
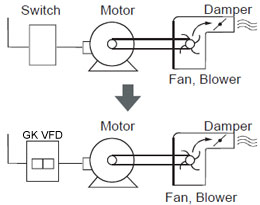
Variable frequency drive in HVAC ...
Variable frequency drives (VFD) have been used for HVAC systems in buildings for more than 40 years. But only in recent years, ...
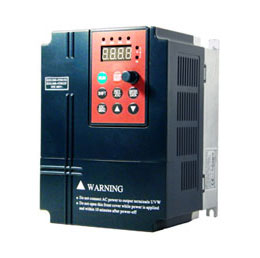
Variable Frequency Drive Harmonics and ...
A discussion of the benefits of variable frequency drives often leads to a question regarding electrical harmonic distortion ...
Three phase inverters
In the variable frequency drive rectifier paper, it explains how to go from three phase alternating current voltage to a direct ...
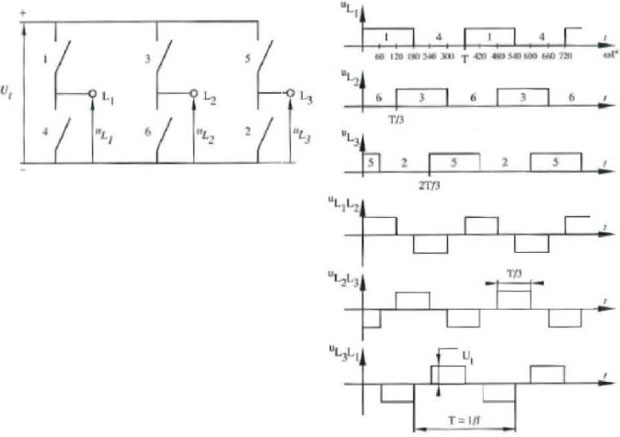
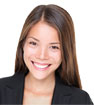
VFD manufacturers

