Disadvantages of Vector VFD
While vector VFDs offer many advantages, they have a few limitations, too.
First, virtually all of today's vector VFDs require tachometer feedback from the motor. The tach increases the price of the AC motor, and there is cost associated with mounting, wiring, and maintaining it. However, brushless VFDs and many DC drives also require tachometer feedback when speed regulation better than 1% is required.
Second, regeneration is more difficult with vector VFDs and with brushless VFDs than with conventional thyristor DC drives. Snubbers, add-on regeneration kits, and common-bus configurations have all been used for regeneration with vector VFDs, but DC drives have the advantage for low-cost, single-section regeneration.
Third, applications which need dynamic braking (slow-down braking without the VFD operating) will require different solutions when vector VFDs are used. DC and brushless VFDs make use of the fact that they can operate as generators without an active regulator to provide a dynamic braking function. Vector (and other AC) VFDs may require DC injection braking or mechanical brakes to provide the functional equivalent of dynamic braking. This is necessary because the regulator on AC VFDs must be active to brake the load.
Finally, a word about motors is appropriate. We noted that "standard" induction motors may be used with vector VFDs. However, the high-performance capabilities of these VFDs can place heavier demands on the motors they power. Special consideration should be given to using motors optimized for constant torque, high-overload duty over a wide speed range. Several manufacturers now offer "vector-duty" motors with tachometer-mounting provisions and blower-cooling. Some companies have gone a step further to design vector-duty motors with lower inertia and special construction features designed exclusively for variable-speed duty.
Vector VFD represents the step forward in performance that many applications have needed to enjoy the advantages of AC technology. It is clear we will see them widely used in new applications. They can also be an alternative to existing mechanical and electrical VFDs.
First, virtually all of today's vector VFDs require tachometer feedback from the motor. The tach increases the price of the AC motor, and there is cost associated with mounting, wiring, and maintaining it. However, brushless VFDs and many DC drives also require tachometer feedback when speed regulation better than 1% is required.
Second, regeneration is more difficult with vector VFDs and with brushless VFDs than with conventional thyristor DC drives. Snubbers, add-on regeneration kits, and common-bus configurations have all been used for regeneration with vector VFDs, but DC drives have the advantage for low-cost, single-section regeneration.
Third, applications which need dynamic braking (slow-down braking without the VFD operating) will require different solutions when vector VFDs are used. DC and brushless VFDs make use of the fact that they can operate as generators without an active regulator to provide a dynamic braking function. Vector (and other AC) VFDs may require DC injection braking or mechanical brakes to provide the functional equivalent of dynamic braking. This is necessary because the regulator on AC VFDs must be active to brake the load.
Finally, a word about motors is appropriate. We noted that "standard" induction motors may be used with vector VFDs. However, the high-performance capabilities of these VFDs can place heavier demands on the motors they power. Special consideration should be given to using motors optimized for constant torque, high-overload duty over a wide speed range. Several manufacturers now offer "vector-duty" motors with tachometer-mounting provisions and blower-cooling. Some companies have gone a step further to design vector-duty motors with lower inertia and special construction features designed exclusively for variable-speed duty.
Vector VFD represents the step forward in performance that many applications have needed to enjoy the advantages of AC technology. It is clear we will see them widely used in new applications. They can also be an alternative to existing mechanical and electrical VFDs.
Post a Comment:
You may also like:
Featured Articles
Variable frequency drive Rectifier
To understand variable frequency drive (VFD) better, it's necessary to explain some of the main parts of the variable frequency ...
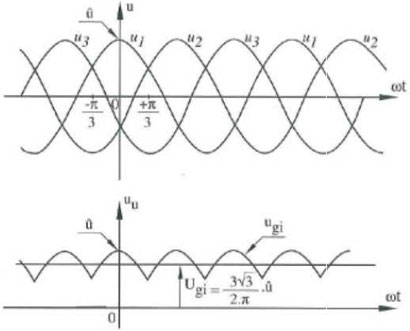
VFD controlled Induction motor ...
This paper presents a procedure to measure the efficiency on an induction motor fed by a VFD by the all operation range to speed ...
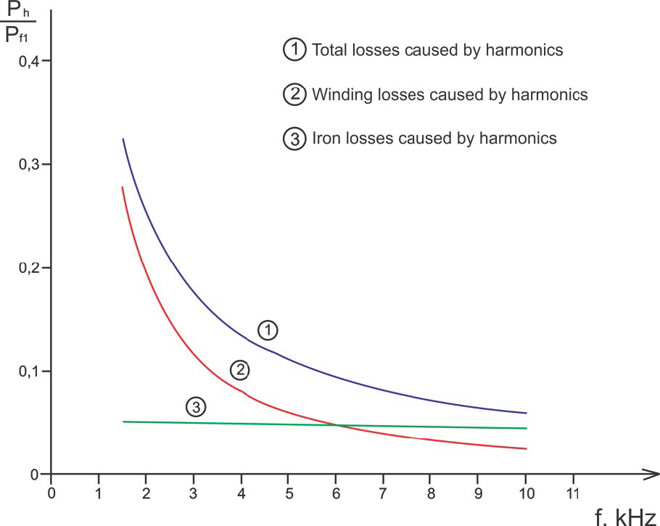
VFD: Pulse Width Modulation (PWM)
Pulse Width Modulation (PWM) VFDs provide a more sinusoidal current output to control frequency and voltage supplied to an AC ...
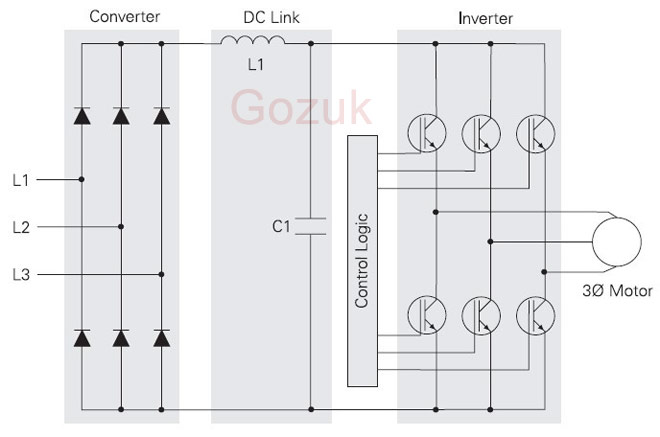
Variable frequency drive Advantages & ...
VFDs are good for variable speed, in a water pump this is used to maintain a steady pressure, they will smooth out variances in ...
Variable frequency drive Energy saving
Energy can be saved in a VFD by reducing the losses in the electric motor or by reducing the energy consumption of the variable ...
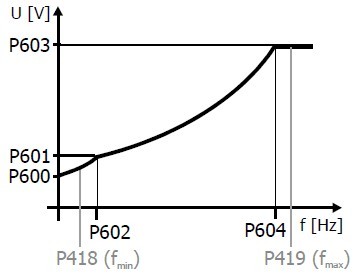
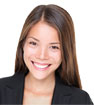
VFD manufacturers

